TM 10-4610-232-12
SECTION II. OPERATORS PREVENTIVE MAINTENANCE
CHECKS AND SERVICES (PMCS)
2-10.
GENERAL. The operators PMCS table lists the inspections and service procedures to properly maintain the
ROWPU in good operating condition. Items covered here are appropriate for operator level only. Always keep in mind the
CAUTIONS and WARNINGS before performing checks and services listed in the PMCS table.
a.
PMCS Table Format. The following columns make up the PMCS table.
(1)
Item No. Each maintenance check is identified by a separate item number. The item column will be used as
a source of item numbers for the TM Number" column on DA Form 2404 Equipment Inspection and Maintenance
Worksheet, in recording results of PMCS.
(2)
Interval. The interval column of the PMCS table identifies when to perform the service check or maintenance.
Before
After
Monthly
During
Weekly
See Procedure for Hours
(3)
Item to Be Inspected/Procedure. This column identifies how to perform the required checks and services.
Carefully follow these instructions. If appropriate tools are not available to operator, unit maintenance should perform the
work. If your equipment does not perform as required, refer to Chapter 3, Section IV. Troubleshooting for possible
problems. Report any malfunctions or failures-to your supervisor or unit maintenance.
(4)
Not Fully Mission Capable If. This column indicates when and why equipment cannot be used after
completing the specific PMCS.
NOTE
If the ROWPU fails to operate, troubleshot with the right equipment. Record any problems
discovered on DA Form 2404 and give to your maintenance supervisor. See DA PAM 738-750.
b.
Special Instructions.
(1)
If the ROWPU must be kept in continuous operation, check and service only those items that can be checked
and serviced without disturbing operation. Make the complete checks and services when the ROWPU can be shut down.
(2)
"Before Operation (B)" checks should be limited to those required for consecutive application by an assigned
operator/crew Perform "Weekly (W)" as well as "Before Operation (B)" PMCS if:
(a)
ROWPU has not been operated since the last weekly PMCS, or;
(b)
ROWPU Is being operated for the first time.
(3)
Leakage definitions for operator/crew PMCS are classified as follows:
Class I
Seepage of fluid (as indicated by wetness or discoloration) not great enough to form drops.
Class II
Leakage of fluid great enough to form drops but not enough to cause drops to drip from item being
checked, inspected.
Class III
Leakage of fluid great enough to form drops that fall from the item being checked/inspected.
CAUTION
Equipment operation is allowable with minor leakages (Class I or II). Consider the fluid capacity in the
Item system being checked/inspected. When in doubt, notify your supervisor.
When operating with Class I or Class 11 leaks, continue to check fluid levels as required by PMCS table.
Class III leaks should be reported to your supervisor.
Change 7 2-34.1 /(2-34.2 Blank)
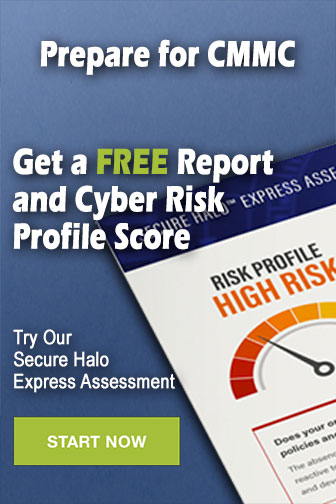