TM 10-4610-232-12
Table 4-2. Unit Troubleshooting Guide (Continued)
MALFUNCTION
TEST OR INSPECTION
CORRECTIVE ACTION
NOTE
Check valve must be installed with the arrow pointing towards the media filter.
Step 3. Check media filter air purge line. Close the air tank block valve and bleed the pressure off the air
manifolds until the air regulator indicates zero pressure. Remove the media filter air purge block valve
from the air manifold and put a pipe plug in the air manifold to replace the valve. Install the air tubing
which was removed to allow removal of the air purge block from the manifold back onto the valve and
close valve. Open the air tank block valve, start and operate the ROWPU and check for air or water leaking
out of the block valve.
If the valve leaks either air or water, replace the media filter air purge block valve (para. 4-68).
Step 4. Check outlet air filter for a buildup of water or white, oily sediment. Open the filter manual drain valve and
watch the end of the tubing attached to it.
If a large quantity of water is blown out, go to Step 6.
Step 5. Check the inside of the filter by removing the top.
If the inside of the filter has a large amount of a white, oily substance, notify direct support
maintenance to clean out the filter and the air blowdown solenoid valve.
Step 6. Check operation of the automatic air blowdown solenoid valve. Operate the air compressor and watch
that the solenoid valve opens and blows down a water/air mixture for about 30 seconds every 15
minutes of air compressor operation time.
(a) If the blowdown valve does not operate as noted above, refer to air blowdown solenoid
troubleshooting.
(b) If the above checks have not isolated the problem, notify direct support maintenance to check the
air storage tank for water and to check the outlet air filter for bypassing.
6. Air pressure cycles rapidly between 1500-1800 psi (10335-12402 kPa).
NOTE
Use soap/water solution when checking for leaks.
Step 1. Check high pressure air lines for leaks.
Notify direct support maintenance if leaks are found.
Step 2. Check air blowdown solenoid for leaks.
Notify direct support if leaks are found.
Step 3. Check the outlet air filter chamber for leaks.
Notify direct support maintenance if leaks are found.
Step 4. Check the air compressor inter-stage relief valves for leaks.
Notify direct support maintenance if leaks are found.
Step 5. Check for low pressure air line leaks.
Repair leaks (para. 4-24).
7. Air compressor runs but discharge does not reach 1700-1800 psi (11713-12402 kPa).
Step 1. Check rotation of compressor motor.
If rotation is wrong, rewire motor by interchanging the T1 and T2 leads in the motor junction box (para.
4-79).
Step 2. Check compressor/motor drive belt tension.
Adjust belt tension (para. 4-78).
Step 3. Check low pressure lines for leaks.
Repair leaking lines or components (para. 4-24).
Step 4. Check all high pressure lines, components, relief valves or leaks.
Notify direct support maintenance if leaks are found
4-28
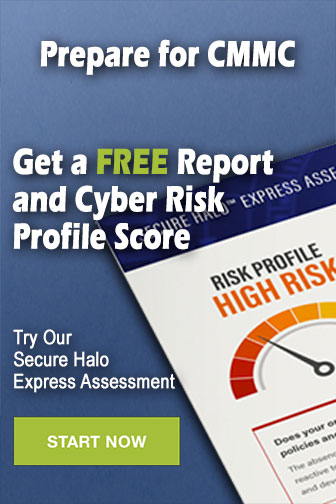