TM 55-1930-209-14&P-1
Section II. Description of operation
13-7 Reverse Osmosis process. The reverse osmosis process separates clean water from salt water or brackish water.
During the natural osmosis process, pure water and saltwater can be separated by a semipermeable membrane In a
container at atmospheric pressure. Because of the difference in salt concentration, pure water will naturally diffuse
through the membrane and raise the water level in the saltwater side as though pressure were being applied to it. The
effective driving force causing this flow is called osmotic pressure. The magnitude of osmotic pressure depends upon the
concentration of dissolved solids in the saltwater and the temperature of the water. The greater the concentration of salt
in the saltwater and the higher the water temperature, the higher the osmotic pressure. To reverse the natural osmosis
process, therefore, pressure is applied to the saltwater side (Figure 13-5). When the applied pressure is greater than the
osmotic pressure, purified water diffuses through the semipermeable membrane from the saltwater side to the freshwater
side. Thus the term reverse osmosis. To use this principle, feedwater is cleaned by several types of filters and pumped
under pressure across semipermeable membranes In the RO block assembly. The resulting purified water, called product
water, flows to the storage tanks. The water on the outside of the membrane that now has a higher salt concentration,
called brine concentrate, is discharged overboard.
13-8 ROWPU system operation. As shown in Figure 13-3, seawater (feedwater) to be processed by the ROWPU's flows
from seawater filters (part of the seawater system) to the pretreatment skid. A flow rate indicator on top of the
pretreatment skid monitors the feedwater's degree of cloudiness and flow rate. In addition, incoming water temperature
may be read on gauge (T1) located in the line on the supply side of the pretreatment skid three-way valves.
The coagulant pump adds coagulant (Hydrapol-50) to the seawater before it enters the seawater filter. Seawater
containing coagulant then flows through the seawater filter to three media filters. The coagulant helps the media filters to
remove fine particles and colloids (clouds of fine particles suspended in water). Normally, a dose of 1.0 ppm is adequate.
Dosage can be increased, however, if a seawater sample taken at valve RO8 contains more impurities than usual.
Dosage is increased by manually adjusting metering pump stroke length and speed.
In the media filters, seawater flows from the top downward. Fine particles and colloids are thus removed from the
seawater so it is suitable for processing by the RO block assembly.
Scale Inhibitor (Hydrapol-100) Is added to the seawater as it is discharged from the media filters and collected into a
single stream. Scale inhibitor limits formation of scale on the RO block membranes. A dose of 4.0 ppm is added to the
seawater by a small, diaphragm type, positive displacement pump similar to the coagulant metering pump. If necessary,
however, dosage can be manually adjusted by changing metering pump stroke length and speed.
Seawater containing scale inhibitor then flows through the cartridge filter assembly on pretreatment skid. The
cartridge filter assembly removes any particles not removed by the media filters that would be harmful to the HP pump.
This filtered seawater then flows to the HP pump where pressure is increased to the 825 psi (maximum) required for
reverse osmosis processing in the RO block.
Pressurized seawater enters RO block inlet manifold which divides the water flow among 16 pressure tubes. Each
pressure tube separates seawater by reverse osmosis into a high purity product water and a brine concentrate stream.
Product water from each pressure tube flows to a common manifold, through a flowmeter, and then through piping to
drinking water tanks or overboard. Normal flow rate as indicated on the flowmeter is 104 gpm. The brine stream from
each pressure tube also flows to a common manifold from which the brine flows through a throttling valve. This throttling
valve allows adjustment of pressure and flow. The adjusted pressure is shown on pressure gauge P5 on the pretreatment
skid. Brine is then discharged overboard through the void 5 port shell.
13-9
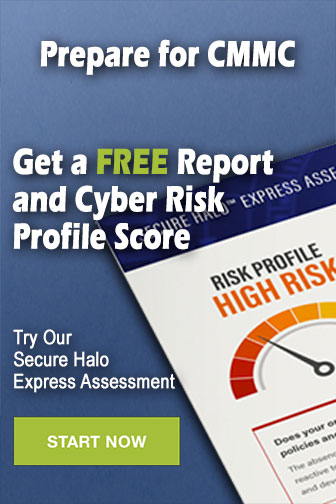