RECOMMENDED PREVENTATIVE MAINTENANCE PROGRAM
FOR
SPANMASTER MOTOR-OPERATED EQUIPMENT
Extended equipment life, best operating characteristics and reduced downtime are the benefits to be obtained from a
continuing preventative maintenance program. The following program is intended for systems in moderate industrial
usage and if usage is heavy or the system is automatic in operation, a more frequent inspection and service routine
should be established.
MONTHLY SERVICE AND INSPECTION ROUTINE
Hoisting Machinery:
1.
Inspect cables for fraying, bends or kinks and lubricate with wire rope compound.
2.
Inspect hook block for worn sheaves or broken sheave flanges.
3.
Check block for loose or frozen bearings and lubricate.
4.
Inspect sheave guards and repair if necessary.
5.
If equipment is floor controlled, check pendent cable for cuts or abrasions that might lead to shorts or
control interruptions.
6.
Inspect strain cables or chains for loose connections and determine that the weight of pushbutton station is
not supported by the electrical cable.
7
Inspect the push buttons for broken or damaged buttons or elements.
8.
Check the oil level in gear case and add if necessary using type and grade as specified by hoist
manufacturer.
9.
Inspect electrical connections for loose connection or damaged wiring.
10
Inspect collectors for shoe wear and alignment and check the electrical connections.
11.
Test brakes for operation and adjust if necessary.
12.
If system is cab-operated and equipped with variable speed controllers, inspect contacts on drum or face
plates for wear or pitting.
13.
Lubricate points of wear and bearings in all controllers.
PMP-1
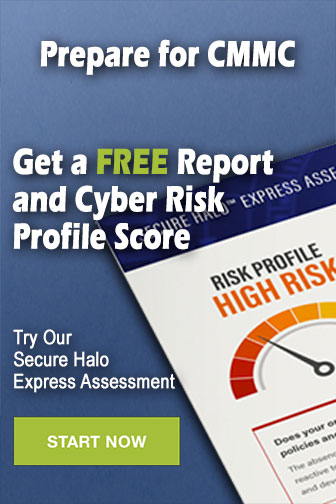