FIGURE 18. CENTRIFUGAL MECHANISM ASSEMBLY
MOTOR REVERSWITCH
When replacing the switch on Models J, L and
R, discard any plastic shims used with the old switch,
Replacement switch includes an appropriate shim, when
required. Be sure to reuse steel bearing retainer.
WEATHERPROOF HOIST
Apply Permatex #2 (or equal) on all mating
surfaces
where
gaskets
are
not
used
when
reassembling.
Check to see that control station gasket and
neoprene grommet are in good condition and in correct
position when reassembling.
GEARING
Models JJ, LL, RR, JJ-2, LL-2 and RR-2 have a
special Liftwheel (S-302), Liftwheel Gear (S-303) and
Intermediate Pinion (S-325). If the gear train in these
hoists is disassembled, the following steps must be
observed in order to properly orient the three parts when
reassembling:
1.
Assemble liftwheel gear to liftwheel. NOTE:
These parts have their splines keyed in such a
way that they will go together, only one way.
See Figure 19.
2.
To install the intermediate pinion, align the
arrows that are stamped on the pinion and lift-wheel
gear so they point toward each other.
3.
Check operation of gear train by rotating the
pinion four (4) complete revolutions; liftwheel gear will
turn one (1) complete revolution and the arrows will
again be aligned as shown. If the arrows do not align or
there is binding between the gear teeth, repeat the
above steps.
4.
For gearing lubrication instructions, see page
16.
FASTENERS
Models A thru H-2, tighten motor housing cover screws
(S-108) to where they have a minimum breakaway
torque of 48 inch pound and the brake attaching screws
(S-253) have 50 inch pound minimum breakaway
torque.
FIGURE 19.
NON-CIRCULAR GEARING.
Models J thru RR-2 tighten limit switch bracket
attaching screws (S-213), motor end bell attaching
screws (S-411), brake attaching screws (S-253) and
hexagonal brake stud (S-265) to where they have a
minimum breakaway torque of 50 inch pound.
LOWER HOOK BLOCK PIN
When removing or installing the lower hook
block pin (S-764), care must be taken so as to prevent
damaging the pin and/or hook block. These pins are
tapered groove pins and as a result they can only be
removed in one direction. To remove the pin, a V-
Block, drift and hammer (or slow acting press) are
required. The drift should be the same diameter as the
pin (5/16" diameter for Models, A, A-2, AA, AA-2, B, B-
2, C, C-2, F, and F-2: and 3/8" diameter for Models J,
J-2, L and L-2) and it should be placed on the small end
of the pin. The small end of the pin is the end opposite
the end on which the 3 grooves are visible. Place the
hook block in the V-Block and drive the pin out using the
drift and a hammer or slow acting press.
To re-install the pin, the parts must be arranged
the same as they were when the pin was removed. To
do this, use the small end of the pin as a gage. First
check the holes in the hook block body and determine
which hole is the largest. Place the hook block body in
the V-Block with the larger hole on top. Next, check
each end of the hole in the lower hook chain block (S-
775) and determine which end is the largest. Place the
chain in the slot of the chain and insert the chain block,
with the large hole on top, into the hook block body.
Align the holes in the hook block body with the hole in
the chain block and insert the small end of the pin in the
hole. Push the pin in by hand until it stops and then use
P hammer or slow acting press to drive the pin into
position so that the end of the pin is flush with the
outside surface of the hook block body.
CAUTION: These are special high strength pins .
and under no circumstances should a pin of a different
material be substituted.
28
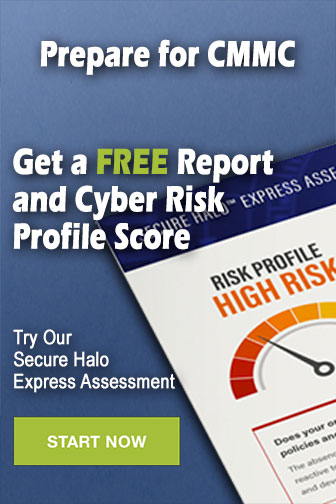