TM 55-1930-209-14&P-13
3-19.2.2.4.2 Test and repair
a. With switchboard circuit breaker P16 closed (ON) and secured, check motor controller input line voltage across
points Al and B1, B1 and Cl, and Al and Cl. If voltage across any terminal pairs is not 440 Vac, power source is
at fault; go to step b to correct problem. If voltage across all three terminal pairs of points is 440 Vac, go to step
c.
b. Check switchboard circuit breaker P16 output line voltage. If voltage across any terminal pairs is 0, circuit
breaker or power source is at fault. If circuit breaker voltage across all three terminal pairs is 440 Vac, replace
faulty power cable from circuit breaker to motor controller.
c. Close motor controller disconnect switch and check line voltage across points A2 and B2, B2 and C2, and A2 and
C2. If voltage across any terminal pair is not 440 Vac, check main contactor contacts. If bad or corroded, clean
or replace contacts. If contacts are good, replace disconnect switch. If voltage across all three terminal pairs is
440 Vac, go to step d to check inputs to main contactor.
d. Check input voltage at main contactor across points L1 and L2, L2 and L3, and L1 and L3. If voltage across any
terminal pairs is not 440 Vac, replace faulty wire(s). If voltage across all three terminal pairs is 440 Vac, go to
step e to check motor controller output voltage.
e. Check motor controller output voltage across points T1 and T2, T2 and T3, and T1 and T3. If voltage across any
terminal pairs is not 440 Vac, go to step f. If voltage across all three terminal pairs is 440, check input voltage at
motor connections T4 and T5, T5 and T6, and T4 and T6. If voltage is not 440 Vac across any terminal pair,
replace faulty wire. If voltage across all three terminal pairs is 440 Vac, replace motor.
f. Open (OFF) and secure switchboard circuit breaker P16. Visually check overload protection thermal units for
burns or damage. If damage is noted, replace faulty overload protection thermal unit. If damage is not noted,
check output voltage of overload protection thermal units across points N1 and T1, N2 and T2, and N3 and T3. If
voltage across any terminal pair is not 440 Vac, replace faulty overload protection thermal unit. If voltage across
all terminal pairs is 440 Vac, go to step g.
g. Check voltage input from 24 Vdc panel to relay K across points D1 and D2. If input voltage is not 24 Vdc, go to
step h. If input voltage is 24 Vdc, go to step i.
h. Check output voltage at power source. If output voltage is not 24 Vdc, troubleshoot power source. If output
voltage is 24 Vdc, check continuity of output wires. If check indicates an open circuit, replace wire(s). If check
indicates a closed circuit, go to step i.
i. Check continuity of relay K3 across points D3 and D4. If connections are good and continuity check indicates an
open circuit, replace relay. If check indicates a closed circuit, and pump does not operate, go to step h. If pump
operates but crane does not operate, go to step n.
j. Check continuity of wires from relay K3 point D4 to overload (OL) contact point W1, from OL point W2 to main
contactor coil point U2, and from relay K3 point D3 to L2. If connections are good and continuity check indicates
a closed circuit, go to step k. If continuity check indicates an open circuit, replace wire.
k. Depress or position the switches listed below and check continuity across points listed. If continuity check
indicates a closed circuit, go to step I. If continuity check indicates an open circuit, replace switch.
Switch position
Across points
Start
START
G1 to G2
Remote station 1
START
Fl to F2
STOP
El to E2
Remote station 2
START
H1 to H2
STOP
11 to 12
AUTO/OFF/HAND
HAND
J1 to J2
3-24
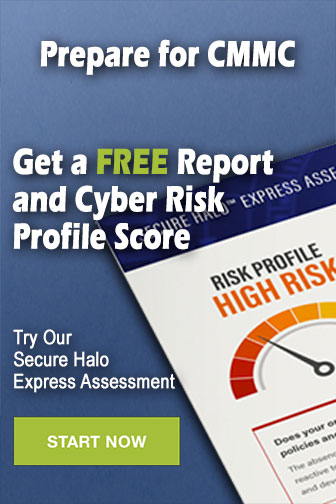