TM 55-1930-209-14&P-15
CHAPTER 5 SANITATION SYSTEMS
Section I. Description and data
5-1 Description. The barge contains two sanitation systems, the ship's toilets and the bilge system. The two systems
are not interconnected.
5-1.1 Ship's toilet functions. The two ship's toilets are located in the ROWPU space; one against the workshop aft
bulkhead, the other in an enclosure on the port side near the stern bulkhead. Ship's toilets are self-contained electric
incinerating disposal systems that reduce human waste to a substance similar to wood ash. Waste is deposited in the
toilets on a waxed paper liner and then incinerated along with the liner in an incineration chamber. This chamber is
cooled during and after incineration by a blower system, which vents to the outside.
The incineration process is begun by pushing a foot pedal. Since the toilet uses no water or chemicals, a bowl liner
must be used with every operation. Waste deposited on this liner is flushed and incinerated automatically when the pedal
is pressed. The indicator lamp on the starboard side lights when the heater is on during the incineration cycle.
Incineration cycle lasts about 20 minutes, during which time the heater switches on and off. The blower, which switches
on at the same time as the heater, force vents the system. It stays on continuously through the cycle until the incinerator
chamber cools to about 140 degrees F. This takes 35 to 45 minutes after the heater and light go off. Onboard installation
is shown on the drawing listed in Appendix A.
5-1.2 Bilge system functions. Bilge system, in the voids, collects and removes equipment waste from the barge and
keeps the bilges dry.
A bilge pump transfers liquid containing oil to the sludge tank. This oily liquid includes bilge water from the voids, waste
lubricating oil from three diesel generators (two ship service generators and one ship auxiliary generator) in void 4 and
waste lubricating oil from two ROWPU HP pump diesel engines in ROWPU space. Bilge water from a void is pumped to
the sludge tank using a portable hose with foot valve to suck up the bilge water. Waste lubricating oil is pumped to the
sludge tank from the generator diesel engine crankcase after a hose is connected between the generator crankcase drain
valve (BD16, BD17 or BD18) and avoid 4 suction valve (BD2 or BD10). Waste lubricating oil is pumped to the sludge tank
from the HP pump diesel engine crankcase drain valves (BD12 or BD13) and valve (9B19) located between the high
pressure pumps.
Liquids containing oil are also drained via gravity to the sludge tank. This oily liquid is drained to the sludge tank from
two ROWPU HP pump spillage catchment drains, fuel oil day tank spillage catchment drains and fuel oil fill station
catchment drain.
The sludge tank holds up to 500 gallons of oil. When this level is reached, the tank's contents must be discharged
offboard (to shore facility or other vessel). When the level in the sludge tank reaches the high level switch on liquid level
indicator, an alarm flashes on the Equipment Monitoring System (EMS) monitor. Audible and visual alarms are triggered
to warn the crew that the sludge tank must be emptied offboard through the shore discharge connection on the starboard
weatherdeck. When bilge tank is full, bilge pump must be started and stopped manually using motor controller above the
pump in void 2 starboard.
The bilge system also drains nonoily liquids, via gravity, directly overboard from spillage catchment drains and deck
drains. This nonoily liquid includes condensation from the workshop heating and air conditioning unit; waste water from
dayroom drinking water fountain and sink; drainage from ROWPU spillage catchment drains, liquids from air compressor
spillage catchment drain, and liquids that collect on deck.
Spillage catchments also contain liquid spills from fuel oil fill station on weatherdeck starboard, deckhouse top fuel oil
port and starboard storage tank and day tank vents, and ship service and ship auxiliary generators. These spillage
catchments are manually drained by opening a ball valve and catching the liquid in a container.
Information about location and function of major components is in Figure 5-1 and Table 5-1. The flow of drainage in this
system is shown in Figure 5-2. Onboard installation and electrical hookup is shown in drawings listed in Appendix A.
5-1
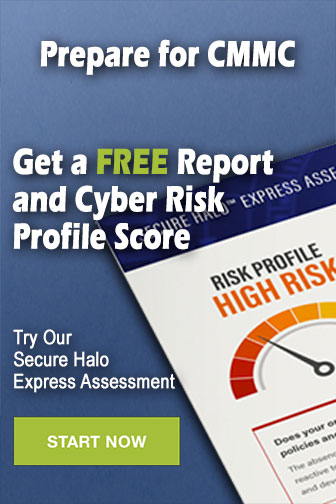