TM 55-1930-209-14&P-21
(7) Remove clutch assembly from lever housing.
(8) Refer to Figure 5-9 if disassembly of field frames, clutch assembly, lever mechanism, etc. Is required.
(9) Remove pipe plugs and oil wicks from end frame, lever housing and drive housing.
5-29 Starting motor cleaning, inspection and repair
a.
Cleaning
(1) Clean all metal nonelectrical parts in cleaning solvent and dry thoroughly.
WARNING
Wear safety goggles whenever using compressed air.
(2) Clean field coils thoroughly with clean cloth dampened with cleaning solvent. Be careful not to damage
insulation coating. Dry thoroughly with compressed air.
(3) Remove dust from armature with compressed air, wipe with a clean cloth dampened in cleaning solvent
and dry thoroughly. Clean armature commutator lightly with No. 00 sandpaper, and remove all traces of copper dust
with low- pressure compressed air.
(4) Clean solenoid insulation plates and nonmetallic washers with a clean cloth dampened with cleaning
solvent and dry thoroughly.
b.
Inspection and Repair
(1) Discard and replace brushes.
(2) Inspect housing and frames for cracks, breaks or other damage. Inspect threads in tapped holes for
damage.
(3) Inspect sleeve bearings for wear, gouges, and grooves. Check for loose fits in housing. If bearing is
loose in bore, replace housing or end cover.
(4) Discard and replace oil wicks.
(5) Inspect armature for grounds, shorts, and open circuits, and replace if damaged.
(6) Use an ohmmeter to inspect field windings in frame for insulation breakdown. Attach one probe of
ohmmeter to frame and other one to field winding terminals. Reading should not be less than one megohm. Replace
defective coils.
(7) Inspect drive pinion for broken or badly worn teeth. Inspect clutch splines for wear or damage. Replace
defective drive pinion.
(8) Inspect shift lever, shaft, and solenoid plunger for cracks or distortion.
(9) Repair by replacement of defective parts.
5-25
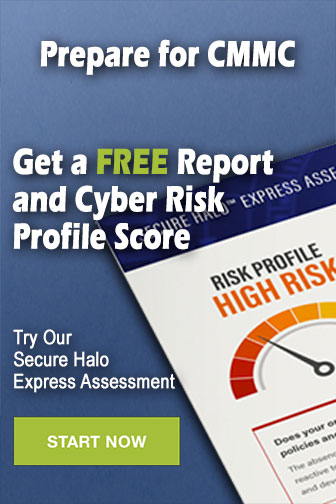