TM 55-1930-209-14&P-21
Section XI. Variable Speed Governor
5-40 General
a.
The variable speed mechanical governor is designed to control engine idle speed, limit maximum no load speed,
and hold engine at any constant speed between idle and maximum as desired by operator.
b.
The governor is a double-weight speed limiting governor and is mounted on right front side of the engine. It is
driven by a shaft that extends through end plate and keys to balance shaft gear.
c.
Two manual controls are provided on governor: a stop lever and a speed control lever. In its normal position,
stop lever holds fuel injector rack near full-fuel position. When engine is started, governor moves injector racks toward
idle speed position. The engine speed is then controlled by movement of speed control lever.
d.
The governor is lubricated by oil splashed from engine gear train. The oil passes through governor weight
housing to shaft and weight assembly. The revolving weights distribute oil to various moving parts of governor. The
surplus oil drains back to engine crankcase through holes in governor bearing retainer.
5-41 Governor operation check
a.
Governor deficiencies are usually indicated by speed variations to engine; however, it does not necessarily mean
that all such speed fluctuations are caused by governor. Therefore, when improper speed variations appear, engine
must be checked as follows before removal and disassembly of governor:
(1)
Make sure governor speed changes are not result of excessive load fluctuations.
(2)
Make sure that all cylinders are firing properly. The deficiency could be in fuel injectors.
(3)
Check for binding in governor operating mechanism or in linkage between governor and injector control
tubes.
b.
With fuel rod connected to fuel injector control tube lever, mechanism must be free from binding throughout the
entire travel of fuel injector racks. If friction exists in mechanism, it can be located and corrected as follows:
(1)
If injector rack sticks or moves too hard, the injector hold-down clamp maybe too tight or improperly
positioned. To correct condition, loosen injector clamp, reposition and tighten to 20-25 lb ft torque.
(2)
A binding injector may be caused by internal dirt accumulation, defective plunger and bushing, or a bent
injector rack. The injector must then be removed, reconditioned and tested.
(3)
An injector rack may bind as a result of an improperly positioned rack control lever. Loosen control rack
adjusting screw. If this relieves bind, relocate lever or control tube and reposition rack as outlined in (4) below.
(4)
The injector control tube may bind in its support brackets, thus preventing free movement of injector racks
to their no-fuel position due to tension on return spring. This condition may be corrected by loosening and realigning
control tube support brackets. If control tube support brackets were loosened, realigned and tightened, then injector
racks must be repositioned as outlined in (3) above.
5-50
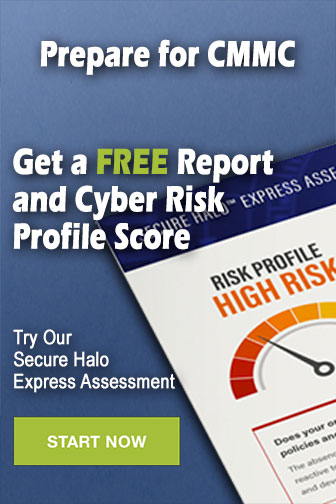