TM 55-1930-209-14&P-3
The coagulant metering pump is a reciprocating, positive displacement unit designed to move specific volumes of
liquid against positive or negative pressure. The pump delivers a manually adjusted dosage of coagulant (Hydrapol-50)
into the feedwater stream before the raw water enters the seawater filter (part of the seawater system) The metering
pump is on top of the pretreatment skid and the ON/OFF switch Is on the control panel Output capacity is adjustable by a
micrometer handknob located on the pump head.
The scale inhibitor metering pump delivers a manually adjusted dosage of scale Inhibitor (Hydrapol-1 00) into the
feedwater stream before the filtered water enters the RO block. Pump description, location, and characteristics are the
same as the coagulant pump.
Four water pressure gauges across the top of the control station monitor feedwater pressure at critical points In its
passage from the seawater pumps to the HP pumps Pressure gauge P1 indicates pressure going into the media filters.
Pressure gauge P2 indicates pressure coming out of the media filters and going into the cartridge filter assembly
Pressure gauge P3 indicates pressure coming out of the cartridge filter assembly. Pressure gauge P5 indicates brine
water pressure as it leaves the RO block Pressure gauge P4, located on the HP pump outlet, measures feedwater
pressure In the HP pump discharge line
The cartridge filter assembly removes any suspended particles that may escape the media filters The filter assembly
housing Is constructed of fiberglass and polyvinyl chloride, and contains 12 polypropylene filter elements whose filtration
rating Is 10 microns During operation, the differential pressure drop across the cartridge filter assembly may be
monitored by subtracting the reading of P3 from P2. A pressure difference of 12 pounds per square Inch (psi) or more
Indicates the need to replace the filter cartridges. Filter replacement Is also Indicated when the green CARTRIDGE
FILTER OK light on the control panel goes out.
1-8.2 Media filters. Three identical media filters are provided for each ROWPU Each filter has a capacity of 120 gallons
per minute (gpm) and all filters are used constantly during water processing Inlet water Is pumped Into the top of the
filters where It is spread out across the filter media and forced downward through four different kinds of media to the
outlet The top layer consists of a layer of relatively coarse, high density anthracite coal Below the anthracite is a layer of
medium fine silica sand The next layer Is fine garnet and below that Is a layer of coarse garnet which covers the radial
laterals of the bottom distributor These four media rest upon a supporting bed of gravel placed In the bottom of the filter
body Media filters require periodic backwashing to remove minute particles collected from the seawater during normal
operation. The need for backwashing Is indicated when the difference between pressure gauges P1 and P2 exceeds 35
psi or when green MEDIA FILTER OK light on control panel goes out Valves on the pretreatment skid control
backwashing and flushing Drinking water production must be stopped while backwashing media filters Because media
materials are progressively denser from top to bottom, they rearrange themselves after backwashing to the original
layers for correct filtering.
1-8.3 HP pump skid. The HP pump skid consists of a steel skid frame with a diesel engine, an HP pump, and a multiple
V-belt drive mounted on It The diesel engine drives the HP pump through the V-belt drive system. The HP pump, In
turn, boosts feedwater pressure from the pretreatment skid to the higher pressure required for the reverse osmosis
process In the RO block assembly. The skid carries all engine accessory equipment such as batteries, exhaust system,
and alternator Diesel engine controls are mounted on top of the V-belt housing.
1-8.4 RO block assembly. The RO block assembly Is a steel skid and frame that supports 16 pressure tube assemblies
and their associated manifolds and piping. The pressure tubes each hold five RO membrane elements Sample valves
are located at the end of each pressure tube for monitoring water quality A product water sample valve is also located in
the piping leading to the drinking water tanks. A flowmeter measures product water flow. A throttling valve In the brine
discharge piping provides a means of controlling product water flow and is adjusted in conjunction with the HP pump
output pressure. The HP pump output is adjusted by varying diesel engine speed to increase or decrease seawater
pressure flowing to the RO block.
1-6
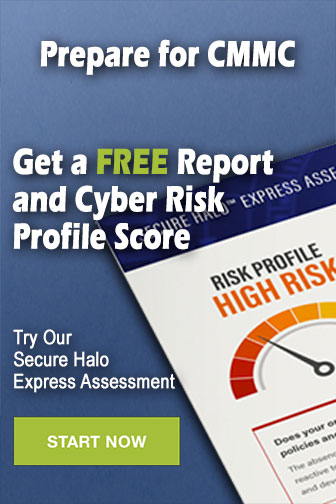