DECKMASTER
FAILSAFE BRAKES
28653
28886
31025
31087
31148
BRAKE FUNCTION
The FaiIsafe Brake is spring loaded to apply the brake and hydraulic pressure is required to release or "hold off" the
brake. Normal operation is to have the brake pressurized in the released position with the vehicle hydraulic system
running. Any function which reduces -e hydraulic system pressure below the release pressure of the brake. will cause a
brake application.
The brake is designed to fit with a gear reducer and a hydraulic motor. The common mounting surfaces of the brake, the
motor, and the gear reducer are machined to close tolerances and should be protected from damage during installation
and removal.
INSTALLATION INSTRUCTIONS (Ref: Fig. 1)
1.
Place the gasket (24) onto the mounting face of the brake.
2.
Place the brake shaft into the gear reducer with the brake bleeder screw in the vertical position.
3.
Move the brake into position with the gear reducer, assuring proper gasket location. Align the mounting bolt
holes by rotating the engaged brake into position. If this is not possible, the brake may be routed after pressure
has been applied to the brake inlet. This will release the brake and allow it to be rotated into position.
4.
Insert the two half-inch bolts (Grade 5) thru the brake, the gasket, and into the threadedhole in the gear reducer
mounting flange. Insure that the bolts are not too long so that they do not bottom out in the reducer before
clamping.
5.
Run bolts in alternately, to prevent binding, until snug. Then torque the bolts to 75-85 lb. ft.
Note: Shafts must slide together freely - DO NOT use bolts to force the units together.
6.
Similarly place the gasket (25) onto the flange of the motor.
7.
Insert the shaft of the motor into the brake and push into position, assuring proper gasket location.
8.
Then insert four half-inch bolts (Grade 5) or two three-eights inch bolts (Grade 5) depending upon the motor
mount being used. Again insure that the proper length bolt is used to avoid bottoming out in the brake.
9.
Run the bolts in alternately, to prevent binding, until snug. Then torque the bolts as follows: Four 1/2 inch bolts
75-85 lb. ft.; two 3/8 inch bolts 31-38 lf. ft.
10.
With motor and brake bolted into position, remove cap plug and connect "inlet" hydraulic line to brake housing - if
not done for shaft alignment Step 3. Brake inlet is .250 tubing O.D., straight thread O-ring boss (438-20 UNF 2B
thread).
11.
Bleed air from brake via bleeder screw.
Note: Maximum pressure to brake...3000 psi.
BRAKE DISASSEMBLY PROCEDURE: (Ref: Fig. 2)
1.
With shaft protrusion downward, disassemble in the following order:
2.
Bolts (23) alternately, Power Plate (21), O-ring (5), Stationary Discs (12), Springs (13), Rotating Discs (11).
Primary Disc 10), Pins (8), Springs (6 & 7).
3.
Further disassembly is not recommended and should not be attempted unless necessary for the replacement of
specific parts, i.e., Snap Rings (1 & 2), Bearing (3) and Shaft (9) from Housing (4). If necessary: proceed as
follows:
A)
Remove Snap Rings (1 & 2). then Shaft (9) with Bearing (3) by lightly tapping the shaft with a plastic millet.
B)
Remove shaft from bearing by supporting the inner race of the bearing and applying pressure to the shaft.
4.
Remove the Piston (14) from the Power Plate (21) by introducing low pressure air - 15 psi - into the hydraulic
inlet. Make sure piston is directed away from the operator. Remove O-rings (16 & 18), and backup Rings (15 &
17) from the piston O.D. and I.D. grooves. Backup Rings will be damaged and should not be removed if
replacement is not planned.
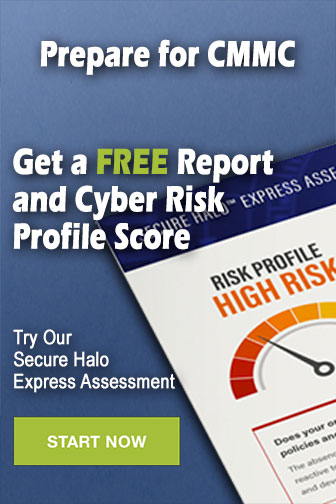