The selection of the proper type of lubricant and lubrication system for spherical roller bearing
pillow blocks is based on a combination of several factors depending on operating temperature,
speed and design conveniences.
GREASE LUBRICATION
Since the simplest design that will accomplish the job is usually the best design, thought should
first be given to the possibility of grease lubrication. Here the factors to be considered are:
1.
Operating temperature should be below 200°F.
2.
Load and speed should be within the limits shown in the "Load-Capacity" tables.
3.
Correct type and grade of grease should be used.
4.
Correct quantity of grease should be applied.
Excess grease in a pillow block may result in high induced temperatures; therefore the quantity
of grease should be kept at approximately 1/3 to 1/2 of the free air space. A regreasing schedule
based on operating conditions should be drawn up and adhered to. For general purpose
applications a grade #2 sodium or lithium soap grease, will provide good service. Because of
the variety of oils, bases and additives used in present day greases, it is not good practice to mix
greases of different types and makes Where contamination or other operating conditions are
severe the Miether Engineering Department should be consulted.
OIL LUBRICATION
Although oil lubrication will allow roller bearings to run at speeds and temperatures higher than
those permissible with grease, is is essential that the following points be observed:
1.
Only high quality petroleum oil should be used.
2.
The oil should have a minimum viscosity of 100 SUS at the operating temperature.
3.
The correct quantity must be applied.
Petroleum oils of poor quality. animal oils and vegetal)!e oils tend to oxidize easily and form
sludge deposits on the hearing parts. In order to provide an oil film of the correct shear strength
an oil with a minimum viscosity of 100 SUS at the operating temperature should be used. As the
viscosity falls below this level the bearing life will be reduced. For example, a bearing running in
a fluid with a viscosity of 25 SUS may be expected to have a life equal to 1 % of calculated life.
The quantity of oil used in roller bearings is quite critical. Too much oil will result in churning and
excess heat. Too little oil will not coat the load surfaces adequately and will result in early
failures. Where a splash system is used the oil level should be maintained at the mid-point of
the lowest roller when the bearing is stationary. Drop feed systems and mist systems should be
adjusted on a flow versus operating temperature basis.
The Oil Selection chart on back page may be used as a guide in selecting the proper oil
viscosity. Find the operating temperature on the bottom scale then go up vertically to or past the
gray line until it intersects one of the slanted lines. For example, at 170° F we would have to go
past the heavy gray line to find the first intersecting slanted line to be number "4". Number "4" is
SAE 40 oil.
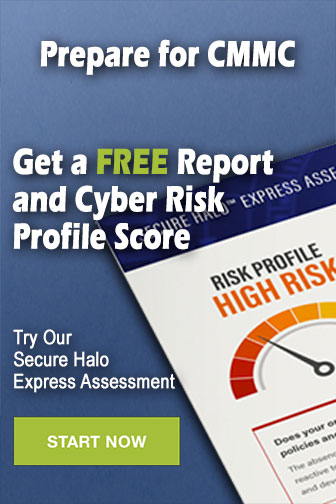