TM 9-4940-342-14&P
4-27. Fuel Control Valve (Thermostat Ad-
justment) (Refer to Fig 2-1)
a. All units have been tested at the factory and
operated
on
the
various
operational
modes.
Temperature valves are given in chapter 2 of this
manual and fuel control valve adjustment will be
required for proper settings. While this control is
extremely reliable, it can be damaged by dirty fuels
(abrasion), water in fuel (corrosion), and deposits on
thermal tube assembly (scale). If scaling is suspected,
the cleaner should be checked for back pressure (see
paragraph 4-9, coil back pressure test).
b. Except for visual checking for scale deposits on
the thermal tube and replacement of complete
control, it is not necessary to remove the fuel control
valve to clean or replace O-ring seals or seat disk.
c. Thermostat should be adjusted by using a small
screwdriver and placing blade into slotted stem on
thermostat. Turn from left to right to decrease
temperature, right to left to increase temperature.
Make small adjustments 1/8 turn or less and allow
for temperature to restabilize before making added
adjustment.
CAUTION
Do not attempt to regulate discharge temperature
by altering fuel pump pressure, nor restricting fuel
oil flow at burner ON-OFF valve. Control with
fuel control valve only.
NOTE
The thermostat is very sensitive and care must be
used not to bend, drop, bump or over adjust it.
4-28. Float Valve Adjustment (Refer to Fig C-6)
The float valve should be set to maintain a water
level of approximately one to two inches below
overflow tube. To adjust, loosen wing screw on float
valve rachet arm and move to next notch, according
to water level required. If notch relocates too high or
too low, gently bend float ball rod arm until desired
setting is acquired.
4-29. Soap Metering Valve Adjustment (Refer to
Fig C-4)
Soap is introduced into the pumping system through
the pump intake check valve and strength is
controlled by the soap control valve. For a stronger
or weaker soap selection at cleaning gun(s) turn
valve handle counterclockwise to increase amount of
soap, clockwise to decrease amount of soap.
4-30. Pressure Regulator Adjustment (Refer to
Fig C-8 and C-13)
a. The pressure regulator is utilized as a backup
control to the excess pressure switch, so in the
event of coil blockage all water is bypassed from
the water pump.
b. Adjust the pressure regulator as follows:
WARNING
Disconnect main power to unit before jumping
pressure switch contacts and removing jumper
after setting regulator.
NOTE
The terminal on the excess pressure switch will
have to be jumped or range increased above 370
psi while setting pressure regulator. Set regulator,
then reset excess pressure switch.
(1) To adjust regulator, loosen adjusting bolt
nut and turn bolt clockwise to increase pressure and
counterclockwise to decrease the pressure. The hex
nut locks adjustment bolt to prevent any rotation
during operation.
(2) The pressure setting should be made as
follows:
(a) Back adjusting bolt out to relieve spring
tension.
(b) Start and run the cleaner at the desired
pressure and temperature.
(c) Close the discharge valves.
(d) Adjust the regulator to 370 psi relieving
pressure per preceding instructions and secure
adjusting locknut.
(e) Open cleaning gun discharge valves,
and reset excess pressure switch to 350 psi setting
and remove jumper wires.
4-31. Air Blower Adjustment (Refer to Fig C-4)
a. The cleaner is equipped with a closed, forced
draft oil burner system and is adjustable by opening
and closing air gate.
b. With cleaner in full operation as a steam
cleaner, loosen clamping screws on sliding air gate
and adjust accordingly.
c. Slide air gate to close opening until dark
smoke appears at heater shell hat opening. Slowly
open air gate until smoke clears.
NOTE
A slight haze is acceptable to excessive cleandraft
exhaust discharge.
d. Tighten clamping screws on sliding air gate
being careful not to move air gate from established
position.
NOTE
If adjustment of air gate fails to correct excessive
smoking, check air blower fan. If dirty, remove
and clean. Also, check for excessively worn or
dirty burner nozzles. Check for proper type of fuel.
23
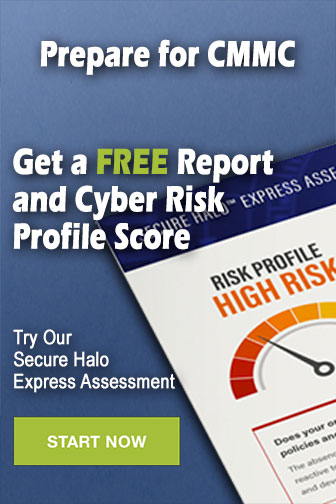