TM 10-4610-232-34
Table 2-1. Direct Support Troubleshooting Guide (Continued)
MALFUNCTION
TEST OR INSPECTION
CORRECTIVE ACTION
Step 3. Check continuity, point-to-point, from J11F to K23(K1). Depress the indicating plungers on K6 and K23
when testing continuity across their contacts.
(a) Repair any loose or damaged wire (para. 2-20).
(b) Replace/repair connector J11 if faulty (para. 2-21).
(c) Replace relay K6 (REF: Interconnection diagram FO-2, Sheet 7) or K23 if their set of contacts does not
show continuity when the indicating plunger is depressed (para. 2-23).
(d) Replace relay K23 if all the above checks have not pin pointed problem (para. 2-23).
Strainer high differential light or horn does not work. (Ref. Schematic diagram FO-1, sheet 9, schematic lines 909-910
and schematic diagram FO-1, sheet 10, schematic line 1006).
NOTE
Refer to malfunctions 7 and 9 for additional troubleshooting. Also, see light test and
alarm circuit troubleshooting.
.
Step 1. Shut down ROWPU and generator. Refer to electrical drawings in Appendix D. Remove the wires from
A3X/A3Y and A2X/A2Y on relay K23 (REF: Interconnection diagram FO-2, Sheet 7). Check for continuity
across each contact with the indicating plunger of K23 out. Push the indicating plunger in and check that
there is no continuity across the contact.
Step 2. Check the wires that were removed in step 1 for looseness or damage at their preceding connections.
Repair any loose or damaged wires (para. 2-20).
Basket strainer light is on and basket strainer is clean or light is not on and strainer is plugged.
Test strainer differential switch (PDSH1) for accuracy. Disconnect J24 (REF: Interconnection diagram FO-2, Sheet
14) from the pressure switch panel. Disconnect the pressure sensing lines from the switch. Remove the cover on the
switch and tag/remove the wires from the pressure switch. Check for internal water leakage. Set a multimeter to the
Ohms x 1 scale and attach the leads to the switch terminals that the wires were on. Connect a dead-weight tester or
another known calibrated pressure control device to the switch high pressure (or inlet) port. The multimeter should
read zero resistance with no pressure on the inlet pressure port. Slowly apply pressure to the switch. The switch
should open on an increasing pressure of 14 to 16 psig.
(a) Replace the switch if there is internal leakage (para. 2-27).
(b) Adjust the switch to the correct setting if it does not actuate as described above. Remove the
adjustment cover and turn the adjuster clockwise to increase the actuation point counterclockwise to
lower it (para. 2-29). Replace the switch if it cannot be adjusted (para. 2-27).
(c) Check the accuracy of the gauge that Ied to this malfunction if the switch is operating correctly.
~ 10. Media filter high differential switch does not work. (Ref. Schematic diagram FO-1, sheet 9, schematic lines 911-9-12).
NOTE
This switch is factory set to open at 25 psig.
NOTE
Refer to malfunctions 11 and 12 for additional troubleshooting.
Step 1. Shutdown ROWPU and generator. Refer to the electrical schematic Appendix D. Check continuity, point-to-
point, from J24A to J24N (REF: Interconnection diagram FO-2, Sheet 14).
(a) Repair any loose or damaged wire (para. 2-28).
(b) Replace/repair connector J24 if faulty (para. 2-28).
(c) Replace PDSH2, if it shows an open circuit (para. 2-27).
2-24
Change 1
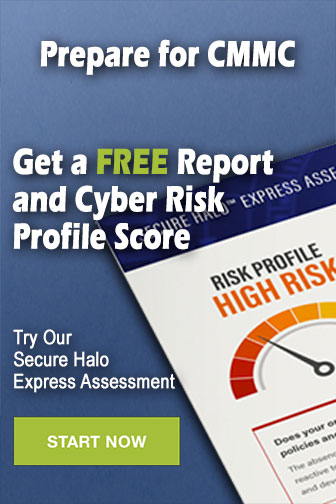