TM 10-4610-232-12
Table 4-2. Unit Troubleshooting Guide (Continued)
MALFUNCTION
TEST OR INSPECTION
CORRECTIVE ACTION
(r)
If the high pressure pump runs but the high pressure pump "ON" light does not work (light test okay) notify direct
support maintenance.
(s)
if the high pressure pump circuit breaker opens whenever the high pressure pump is started, notify direct support
maintenance.
(t)
If the high pressure pump overload heaters trip open continuously, notify direct support maintenance.
(u)
If the high pressure pump starts but the van lights go out or dim considerably, notify direct support maintenance.
(v)
If the carbon monoxide monitor does not read "60" as a final value during span test, notify direct support
maintenance.
(w)
If the carbon monoxide monitor does not read zero during the zero test, notify direct support maintenance.
(x)
If the media filter backwash cycle does not work properly, notify direct support maintenance.
SAFETY VALVE.
Safety valve does not work (Reference Schematic Diagram FO-1, sheet 8, schematic line 822).
Step 1.
Shutdown ROWPU. Shutdown generator. Open the condulet attached to the safety valve solenoid valve. Remove
tape and disconnect wire connectors. Check the solenoid for resistance across its leads.
If there is no resistance or shows an open circuit, replace the solenoid valve (para. 4-51).
Step 2.
Check wires from solenoid condulet box back to control panel TB1-67 and TB1-77 for continuity.
(a) Replace the cable if any wire does not show continuity or if the wires are shorted (para. 4-27).
(b) If the cable check is okay, notify direct support maintenance to troubleshoot control panel wiring.
PUMP HEAT LAMPS.
Hypochlorite mixer does not work. (Reference Schematic Diagram FO-1, sheet 8 schematic line 820).
Step 1.
Remove connector P54 from the bottom of switch panel No. 2 (para. 4-31). Check for 110-120 VAC between J54A
and J54B (Reference Interconnection Diagram FO-2, sheet 15) with MIXER switch "ON'.
If voltage is not present, go to step 3.
Step 2.
Remove and tag the wires to the mixer motor. Check the cable and connector for continuity and shorts on each
wire.
(a) Replace the cable assembly if open or shorted (para. 4-39).
(b) Replace the mixer motor if the cable check is okay (para. 4-39).
Step 3.
Remove connector P52 from the side of the switch box 2. Check for 110-120 VAC between P52B and P52J
(Reference Interconnection Diagram FO-2, sheet 15).
If voltage is not present, go to step 5.
Step 4.
Check continuity, point-to-point, from J52B to J54A and from J52J to J54B.
(a) Repair any hose or damaged wire (para. 4-31).
(b) Replace switch SS4 (Reference Interconnection Diagram FO-2, sheet 15) if open (para. 4-31).
(c) Replace either electrical connector assembly if faulty (para. 4-31).
Step 5.
Remove connector P12 (Reference Interconnection Diagram FO-2, sheet 15) from the side of the main control
panel. Check for 110-120 VAC between J12B and J12J (Reference Interconnection Diagram FO-2, sheet 9).
If voltage is not present, notify direct support maintenance.
Step 6.
Check continuity from P12B to P52B and from P12J to P52J.
Replace the cable if open (para. 4-27).
Change 1 4-37
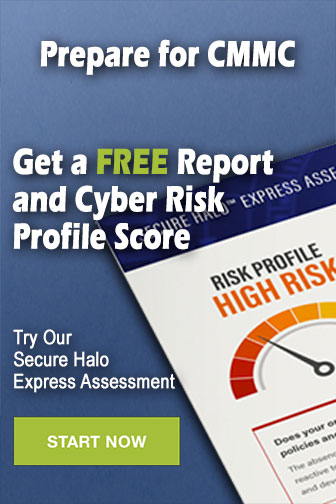