T M 1 0 4 6 1 & 2 3 2 - 1 2
Table 4-2. Unit Troubleshooting Guide (Continued)
MALFUNCTION
TEST OR INSPECTION
CORRECTIVE ACTION
AIR BLOWDOWN SOLENOID.
Air blowdown solenoid valve does not work schematic lines 826-827).
Step 1.
Step 2.
Step 3.
Step 4.
Shutdown the ROWPU. Open the control panel and power up the unit. Open the air manifold drain
valve and bleed air off the air manifold until air pressure is less than 1000 psig (6895 kPa). Start the air
compressor and watch TDK1 (Reference Interconnection Diagram FO-2, Sheet 8). The outside indi-
cater should be set on 15 and the inner dial should be somewhere between 15 and zero. The inner
indicator should move down towards zero as the aircompressor runs. When the inner indicator gets
somewhere below 1 the timer should supply voltage to the solenoid valve for about 30 seconds. It will
then reset to 15 and start the process over.
If the timer does not operate as noted above, notify direct support maintenence.
Disconnect connector J28 at the high pressure solenoid valve. Check for 110-120 VAC across pins
J28A and J28B Reference Interconnection Diagram FO-2, Sheet 14) during the time period noted in
step 1. (Timer TDK1 can be reset to a lower time cycle during testing to speed up the process. It must
be reset to 15 when testing is over.)
(a) If there is no voltage during the last 30 seconds of the time cycle, go to step 3.
(b) If there is voltage, notify direct support maintenance to replace/repair the high pressure air
blowdown solenoid valve.
Disconnect connector P13 (Reference Interconnection Diagram FO-2, Sheet 14) from the control
panel. Check for 110-120 VAC across J13T and J13U (Reference Interconnection Diagram FO-2,
Sheet 9) during the last 30 secords of the timer cycle.
If voltage is not present, notify direct support maintenance.
Check continuity from P13T to J28A and from P13U to J28B.
Replace the connectors and cable if continuity is not present as noted (para. 4-27).
F L O W M E T E R S
1. Flowmeter(s) do not show flow (Reference Schematic Diagram FO-1, Sheet 8, schematic lines 815-819).
Step 1. I
Step 2.
Remove the flow sensor for the inoperative meter from the piping. The feed flow sensor is located on
the front wall piping, the waste sensor is located on the ceiling
next to the control panel, and the prod-
uct sensor is on the back wall piping behind the control panel. Check the paddle wheel for debris and
ease of rotation.
a) Use a stiff brush and remove any debris that maybe sticking to the wheel.
b) lf the paddle wheel cannot be cleaned up so that it spine very easily, notify direct support
Watch the flowmeter and spin the paddle wheel on the flow sensor. The flowmeter needle should rise
as the paddle wheel is spun vigorously in the right direction.
Notify direct support maintenance if the meter does not indicate flow.
2. Flowmeter is inaccurate.
Notify direct support maintenance.
W A R N I N G
Electrical high voltage can cause serious injury or death. Some tests performed in
troubleshooting require power to be connected. Always take proper measures to en-
sure personal safety.
Change 1
4-73
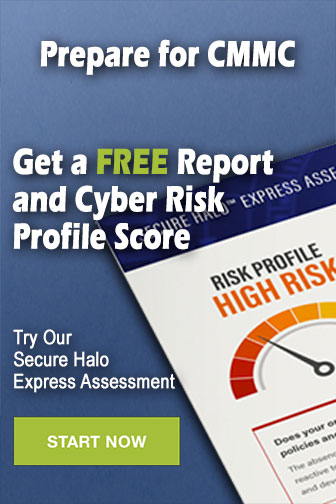