TM 55-1930-209-14&P-1
CHAPTER 13 ROWPU SYSTEM
Section I. General
13-1 General. The ROWPU system processes seawater or brackish water into drinking water. Normally, this system
processes seawater supplied by the seawater system discussed in Chapter 11, and creates product water. Chlorine is
then added to this product water by the chlorination system discussed in Chapter 9. The resultant drinking water is
discharged into four storage tanks that are part of drinking water system described in Chapter 14.
13-2 System description. The ROWPU system has two identical units, ROWPU 1 and ROWPU 2, that process
feedwater (seawater or brackish water from a river or lake) provided by the seawater system discussed In Chapter 11.
This ROWPU system produces two products; brine water or dirty water that is dumped overboard and highly filtered
nonsaltwater called product water. The product water, with the addition of chlorine from the chlorination system described
in Chapter 9, becomes drinking water. Drinking water is pumped either into the drinking water system's four drinking
water storage tanks or directly overboard Components of the ROWPU system are listed in Table 13-1. Location of
ROWPU 1 components is shown in Figure 13-1 and ROWPU 2 components in Figure 13-2. A block diagram of the
ROWPU system is shown in Figure 13-3. Equipment specifications, maintenance information, and manufacturer's service
manuals are contained in TM 55-1930-209-14&P-3.
13-3 Component description ROWPU system main components are described below. Main components are shown in
figure 13-4. Valves, controls, and indicators are discussed In paragraph 13-9.
13-3.1 Pretreatment skid assembly. The pretreatment skid assembly controls water flow and monitors water processing
from the seawater pumps through various cleaning procedures before water is delivered to the HP pumps. This assembly
consists of a control station, two chemical metering pumps for adding coagulant and inhibiter, four water pressure gauges,
a cartridge filter assembly, interconnecting piping, and valves. Seawater pumps, part of the seawater system, establish
the required flow rate through the pretreatment skid, the cartridge filter assembly, and the media filters.
The control station contains electrical circuitry for operating one seawater pump and two chemical metering pump
motors. It also mounts the seawater pump OFF/ON/START switch; OFF/ON switch for each chemical metering pump;
BACKWASH TIMER; and POWER ON, CARTRIDGE FILTER OK, and MEDIA FILTER OK indicator lights.
The coagulant metering pump is a reciprocating, positive displacement unit designed to move specific volumes of
liquid against positive or negative pressure. The pump delivers a manually adjusted dosage of coagulant (Hydrapol-50)
into the feedwater stream before the raw water enters the seawater filter (part of the seawater system). The metering
pump is on top of the pretreatment skid and the ON/OFF switch is on the control panel. Output capacity is adjustable by a
micrometer handknob located on the pump head.
The scale inhibitor metering pump delivers a manually adjusted dosage of scale inhibitor (Hydrapol-100) into the
feedwater stream before the filtered water enters the RO block. Pump description, location, and characteristics are the
same as the coagulant pump.
Four water pressure gauges across the top of the control station monitor feedwater pressure at critical points in its
passage from the seawater pumps to the HP pumps. Pressure gauge P1 indicates pressure going into the media filters.
Pressure gauge P2 indicates pressure coming out of the media filters and going into the cartridge filter assembly.
Pressure gauge P3 indicates pressure coming out of the cartridge filter assembly. Pressure gauge P5 indicates brine
water pressure as it leaves the RO block. Pressure gauge P4, located on the HP pump outlet, measures feedwater
pressure in the HP pump discharge line.
The cartridge filter assembly removes any suspended particles that may escape the media filters. The filter assembly
housing is constructed of fiberglass and polyvinyl chloride, and contains 12 polypropylene filter elements whose filtration
rating is 10 microns. During operation, the differential pressure drop across the cartridge filter assembly may be
monitored by subtracting the reading of P3 from P2. A pressure difference of 12 psi or more indicates the need to replace
the filter cartridges. Filter replacement is also indicated when the green CARTRIDGE FILTER OK light on the control
panel goes out.
13-1
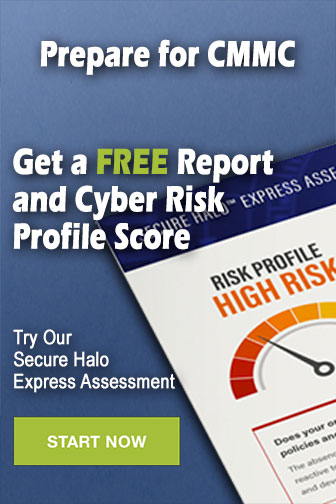