TM 55-1930-209-14&P-11
(6) Increased Inspections. Perform weekly as well as Before Operations PMCS if:
(a) You are the assignedoperator and have not operated the item since the last weekly PMCS.
(b) You are operating the item for the first time.
(7) Leakage definitions. In checking for fluid leaks, the following leakage definitions apply to all ROWPU barges
and barge equipment, product water, and seawater leakage by class type.
(a) Class I - Seepage of fluid (as indicated by wetness or discoloration) not great enough to form drops.
(b) Class II - Leakage of fluid great enough to form drops, but not enough to cause drops to
drip from the
item being checked/inspected.
(c) Class III - Leakage of fluid great enough to form drops that fall from the item being checked/inspected
CAUTION
Equipment operation Is allowable with minor leakages (Class I or II). However, the
fluid level or operating pressure of the item being checked/inspected must be
considered. When In doubt, notify the shift leader or bargemaster.
When operating with Class I or Class II leaks, continue to check fluid levels as
required by PMCS and operating Instructions.
(8) The following fuel and hazardous material leakage procedures apply for any fuel, chemical, or bilge system.
WARNING
Class I, II or III leaks or seepage occurring In a fuel, chemical, or bilge container,
tank, line, piping, or valve can cause fire or health hazards.
(a) If any leaks or seepage from a fuel, chemical, or bilge container, tank, or fluid line is detected, it must be
immediately reported to the shift leader or bargemaster for corrective action.
(b) To prevent combustible or toxic fumes from collecting or contaminated material from spilling, exercise
extreme caution after detecting leaks or seepage of flammable or hazardous material.
c. Continuous operation. When equipment must be kept in continuous operation for extended periods of time,
check and service only those items that can be checked and serviced without disturbing operations. Perform
complete checks and services when the equipment can be shut down.
d.
Maintenance log. Always record the time and date of PMCS, any deficiencies noted, and corrective action taken
in the PMCS log book
C-2
Major components. The equipment monitoring system consists of the alarm/casualty monitoring
equipment, two 12 V dry cell batteries, a battery charger, two strobe lights, two horns, and a buzzer. The
alarm/casualty monitoring equipment consists of various sensors and switches, a main processor, keyboard, video
monitor, alarm relay module, main power switch, and bilge alarm module.
C-3
Equipment Monitoring System Description . This system can accept information from as many as 168
different inputs. On the barge, however, only 39 are used. The keyboard and video monitor make up the station from
which an operator selects and views any page of monitored information, acknowledges alarms and sets or changes
alarm conditions. The system is designed to operate between 32 and 131 degrees F
C-2
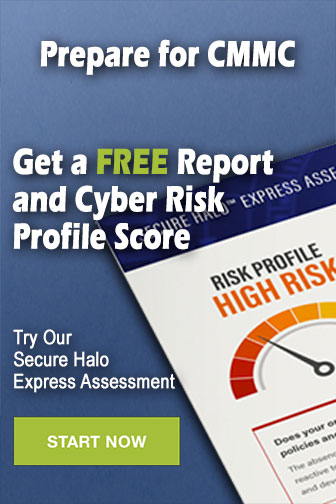