TM 55-1930-209-14&P-14
2-19.3.1.2 Repair
a.
Removal
(1) Remove manual release knob (148), housing nuts (15) and housing (7) (see Figure 2-7).
(2) Disconnect solenoid wires.
(3) Depress solenoid plunger (29) and pull release rod (146) back to lock brake mechanism in manual release
position. Tie plunger (29) to frame (79) when manual release rod (146) is not provided.
(4) Remove entire support plate assembly (142) by evenly unscrewing screws (142S). Remove screws and
lockwashers (142W).
(5) Remove pressure plate (5), friction disc (4), and stationary disc (3).
(6) Remove hub (16) and key by unscrewing set screws (16S).
(7) Remove endplate (2) from end of motor unscrewing four 1/2-13 socket head cap screws.
b.
Repair and adjustments. Before installing the electric brake, if necessary replace the solenoid coil, friction discs,
or solenoid lever and pinion assembly and reset the brake as follows:
(1) Replace solenoid coil as given in paragraph IV, A in the Stearns service manual in Appendix B.
(2) Replace friction discs as given in paragraph IV, B in the Stearns service manual in Appendix B.
(3) Replace solenoid lever and pinion assembly as given in paragraph IV, E in the Stearns service manual in
Appendix B.
(4) The solenoid is factory set with a 3/4 in. to 15/16 in. air gap, and requires no resetting, even when changing
friction discs. The gap is determined by the position of wrap spring stop (76) (see Figure 2-). Due to wear-in
of parts the normal operating gap is 11/16 in. to 1 in. If (stop) screw (76S) has been loosened and
retightened, the air gap may require resetting. Should the air gap need adjusting, reset as follows:
(a) Measure air gap between mating surfaces of plunger (29) and solenoid frame (79). Increase by raising
slightly, or decrease by lowering slightly, wrap spring stop (76). Be sure to retighten (stop) screws (76S).
Manually lift plunger to maximum travel and release. Depress plunger, manually, repeat several times,
then recheck air gap.
(b) Make sure tang of wrap spring (71) is below, and contacts with wrap spring stop (76) when solenoid lever
(28) is manually raised. If stop is bent outward, allowing tang to bypass it, rebend to square position,
assemble correctly, and reset solenoid air gap as described in step (a).
c.
Installation
(1)
Attach endplate (2) (see Figure 2-4) to the end of motor using four 1/2-13 socket head cap screws, torque per
manufacturer's specifications.
NOTE
Head of screws must not project above friction surface.
(2) Position hub (16) and key on the motor shaft so outboard face of hub will protrude approximately 1/32 in. to
1/16 in. beyond face of the last outboard friction disc.
2-18
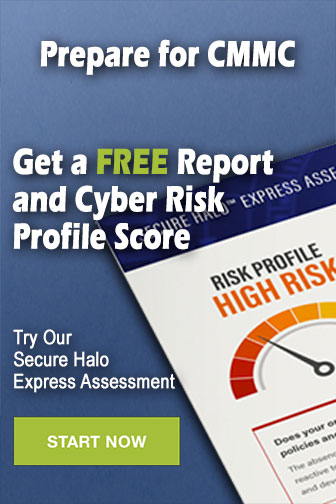