REPAIR INSTRUCTIONS
LEAK TESTING
Leaks in any refrigerating system may be caused by careless usage or during shipment. The smallest leak will eventually
cause failure of the refrigerating system. A trace of oil found around a connection indicates that there is a leak at this
point and steps should be taken to test and repair it.
A Halide torch is used to detect a leak on a condensing unit Freon 12 refrigerant. It is necessary that the copper heat
plate in the torch be red hot during the test. Pass the pick up tube very slowly around all sides of the Joint to be tested.
As Freon is heavier than air, it is usually easier to find a leak Just below the suspected area. A change color in the flame
from blue to green indicates a leak.
EXPANSION VALVE REPLACEMENT
To replace an expansion valve, the condensing unit has to be pumped down as explained. Care must be taken so that no
moisture enters the open lines. Allow the evaporator to defrost and wipe off all moisture around the flare nuts with Carbon
Tetrachloride. Replace the valve and tighten down the falre nut. When a system has been opened, it is a safe policy to
change the dehydrator at the same time in event some moisture entered the system. Charge the system as explained in
refrigerant charging.
The expansion valve for this model is listed on the material list. When replacing an expansion valve, use exact
replacement. Keep the adjustment cap on the valve when the machine is in operation. This prevents moisture from
accumulating in the diaphragm and freezing.
TEMPERATURE CONTROL REPLACEMENT AND ADJUSTMENT
The control has an adjustment for any slight variation in compartment temperature that may be required. At no time,
except for servicing or replacement purposes should the adjustment be moved. The control is pre-set to operate at a
specific temperature range.
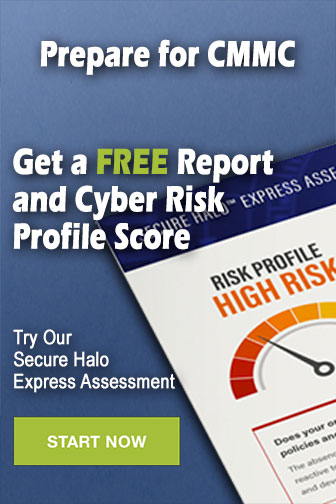