TM 55-1930-209-14&P-21
b.
Test. If inspection does not reveal any external damage, make a series of tests to determine condition of
injector to avoid unnecessary repair. An injector that passes all tests outlined below is considered satisfactory for
service. Test fuel injector as follows:
(1)
Control Rack and Plunger Movement Test
(a)
Place injector in injector fixture and rack freeness tester. Then, place handle on top of injector
follower.
(b)
If necessary, adjust contact screw in handle to insure contact screw is at center of follower when
follower spring is compressed.
(c)
With injector control rack held in NO FUEL position, push handle down and depress follower to
bottom of its stroke. Then, very slowly release pressure on handle while moving control rack up and down, until follower
reaches top of its travel. If rack does not fall freely, loosen injector nut, turn tip, then retighten nut. Loosen and retighten
nut several times if necessary. If rack isn't free, change injector nut. Generally, this will free rack. In some cases it may
be necessary to disassemble injector to eliminate cause of misaligned parts.
(2)
Valve Opening Pressure Test. The purpose of this test is to determine relative pressure at which
injector valve opens and fuel injection begins. The test is performed in injector test fixture. Place injector in tester as
shown in Figure 5-13 (1 of 3). Locate adaptor plate on top of support bracket by positioning the 3/8 inch diameter hole at
far right of adaptor plate onto 3/8 inch diameter dowel pin. Mount injector through large hole and insert injector pin in
proper locating pinhole.
WARNING
Always place injector in proper position in relation to spray deflector before it is tested, in order to
prevent fuel spray from penetrating skin. Fuel oil which enters blood can cause serious infection.
(a)
Refer to Figure 5-13 (2 of 3). Purge air from tester and injector system by moving lever 4 down
and operating pump lever 1 until bubbles no longer appear in clear discharge tubing.
CAUTION
Do not overtighten nut or nut on seal will be damaged.
(b)
Close thru-flow valve to allow pressure to build in gage 1.
(c)
With fuel rack in FULL FUEL position, operate pump lever 1 rapidly until valve opening pressure
of 450 to 850 psi is reached and spray tip holes are open by pattern of spray produced. If valve opening pressure is not
within 450 to 850 psi range when spray pattern occurs, see troubleshooting chart, Table 5-1.
5-33
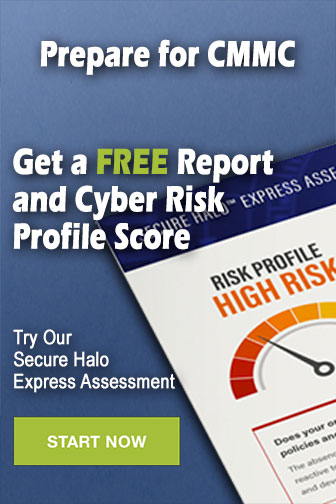