COFLEXIP & Services Inc.
In drilling, it outperforms both
hose and pipe with swivel joints
Coflexip flexible pipe lowers costs
and raises the safety factor on
drilling rigs.
Coflexip initially costs more
than other Alternatives for choke
and
kill
lines,
cementing/acidizing/fracking lines
and other drilling jobs. But it lasts
so much longer that the cost is
actually lower in the long run.
That's based on the materials cost
alone. If the downtime cost
avoided by a line that lasts longer
is included, Coflexip is cheap
compared to other solutions.
For many jobs, Coflexip is a
lot safer than rubber or pipe with
swivels because of its strength,
durability,
and
corrosion
resistance. What price can be put
on that?
Our
literature
on
drilling
applications tells exactly how and
where Coflexip can save you
money.
Actually tougher than rigid steel
pipe
In comparison to API 5LX steel
pipe, Coflexip flexible steel pipe
generally
has
better
abrasion
resistance,
better
corrosion
resistance, and better resistance to
vibration and flexing fatigue.
It requires less maintenance in
most
applications
and
it
is
compatible with more chemicals,
including H2S.
Compared to reinforced rubber
hose, Coflexip has greater crush
strength,
abrasion
resistance,
ultraviolet resistance, and flexing-
fatigue resistance. It stands up to
a
wider
range
of
chemicals,
including H2S, and suffers almost
no aging damage.
Coflexip works because of a
unique design
Coflexip is a unique combination
of
high-strength
steels
and
thermoplastic.
In the basic Coflexip construction,
the carcass of interlocking Z-
section steel handles the radial
loads, including internal pressure,
and keeps the pipe
Crush strength of Coflexip pipe is
demonstrated
by
parking
a
truckload of drill pipe on a piece of
rotary hose. The pipe remains
perfectly round under the 9.000-lb.
direct load.
from
kinking
or
collapsing.
Alternating spiral layers of heavy
steel wire handle the tension loads
and
give
the
pipe
a
tensile
strength comparable to rigid pipe.
Outside
and
inside,
thermoplastic layers protect the
steel
components
against
corrosion and make the pipe
leakproof. There is no bonding
between layers. When the pipe
bends, each layer
The interlocking spiral of steel -
section is the structural element
that withstands radial loads from
internal and external pressures.
and keeps the pipe from kinking.
moves independently. That's why
the fatigue resistance of Coflexip
is much higher than that of
reinforced hoses.
For most drilling applications.
the outer thermoplastic layer is
covered with a stainless steel wrap
for
extra
protection.
For
production applications, an extra
stainless steel layer goes on the
inside, to prevent damage from
TFL tools.
That's
the
basic
structure.
Dozens
of
Coflexip
structures
have been developed for specific
applications in sizes from I to 22
inches I.D., with working pressures
up to 15,000 psi, and continuous
lengths of more than one mile.
There is no bonding between
layers in the Coflexip structure as
there
is
in
the
structure
of
reinforced rubber hose.
That's why Coflexip has such
extreme' high resistance to flex
fatigue. Four inch Coflexip pipe
has withstood 1,600,000 flexing
cycles
under
a
10.0(0
psi
maximum working pressure before
failure due to the unnaturally
induce temperature of +1001°C.
A long list of uses
Since 1972, Coflexip has been
successfully used in almost every
major oilfield in the world. In the
Gulf of Mexico and onshore, it
serves as:
· Offshore platform risers
Subsea flowlines
Jumper lines
Subsea mudslide protectors
Vent and flare lines
Temporary production systems
Permanent production systems
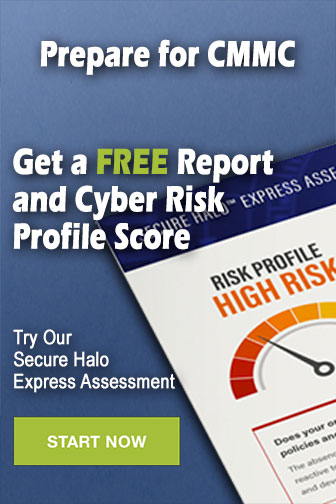