3 Optional dual control instructions
(DIRECTAIR) 5 through 15 HP single-stage units are available
with pneumatic dual control. This option allows operation to
meet air demand. When air requirements are average the
"auto" mode of operation is suggested. When air demand is
high, the "constant" mode of operation may be used.
The main components of the dual control system are the
pressure switch and the pilot valve. In the auto mode of
operation, the compressor is regulated by the pressure switch.
When air pressure reaches the preset upper limit of the
pressure switch the unit will unload and shut down. When tank
pressure drains to the lower limit of the pressure switch, the
unit will start up and begin pumping again In the constant
mode of operation, the compressor is regulated by the pilot
valve. On the top of the pilot valve is a control knob.
By turning this knob counter-clockwise, tank pressure is
allowed to flow through it. The unit will pump until the preset
upper limit of the pilot valve is reached. At this time, the unit
will remain running however, the compressed air is vented to
the atmosphere instead of flowing into the tank. When tank
pressure decreases to the lower pressure limit the unit will
again pump air into the tank.
To return to the stop/start mode of operation, simply turn the
control knob on the pilot valve clockwise.
Warning: The pressure switch and pilot valve are preset to
specified settings. These settings must not be altered.
4 Maintenance schedule
Routine maintenance insures trouble-free operation and
protects your investment. All warranties are void if
maintenance is neglected.
Daily:
1.
Check oil level, which should be in lower half of the
sight glass. Add, if necessary, using oil mentioned
Initial start-up"
2.
Turn off power at main fuse box and drain moisture
from tank by opening the drain cock in the bottom of
the tank.
Weekly:
1.
Remove and clean air intake filter with compressed
air Replace if necessary.
2.
Turn off power and clean dust and foreign material
from entire unit
Monthly:
1.
Test operation of safety valve by pulling the test link.
Air from the tank should escape. If it does not,
replace the safety valve. This valve cannot be
adjusted.
Note: In the event the unit ran over pressure, this
safety valve would reduce tank pressure to a safe
level. Be sure it will work properly. Never run the
unit without this safely valve.
Every six months or after 1000 hours [max I of operation:
1.
Change the lubricating oil
2.
Check overall operation of unit. It should be as
described in these instructions. A sudden change in
performance indicates a problem developing, and
should be investigated
Warning: Do not use petroleum based or other flammable
solvents for cleaning.
5 Trouble shooting
Condition
Possible faults
Suggested remedy
1.
Compressor does not start
a.
No electrical power
a.
Check or have electrical system checked
b.
Receiver pressure between starting and
b.
Wait until pressure drops
stopping pressures
c.
Coupling sleeve damaged
c.
New sleeve
2.
Compressor does not pump
a.
Unloader jammed
a.
Disassemble and clean unloader
b.
Solenoid valve not energized
b.
Have electrician check wiring
6
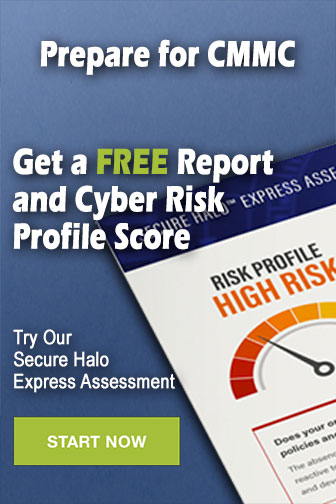