TM 55-1930 209 14&P-91
Table C-1. Preventive Maintenance Checks and Services for Electrical Power Systems (Continued)
B - Before
D - During
A - After
H - Hourly Interval
Interval
Procedures:
Equipment Is
Item
Item to be
Check for and have repaired
Not Ready/
No.
B D
A
H
Inspected
or adjusted as necessary
Available If:
6) Open engine bilge drain valve BD18 and
set valves as follows:
(a) Open valves BD7 and BD11.
(b) Close valves BD1 thru BD6, BD8 thru
BD10, and BD14.
7) Start bilge pump by turning on bilge pump
controller. Controller is on void 2
starboard bulkhead above bilge pump.
8) When oil has been pumped out of
crankcase, simultaneously close valve
BD18 and turn of bilge pump.
9) Disconnect bilge utility hose, clean, and
return to storage in void 5.
10) Unscrew cylindrical oil filter element by
turning from right to left. Discard old
filter element.
11) Clean oil filter housing and lip where oil
filter element fits into housing. Make
sure all of old gasket is removed and
gasket seat on housing is clean.
12) Lubricate new gasket with clean oil.
Place on seat of new filter element.
Screw on new filter element until gasket
contacts base of filter housing. Hand
tighten filter an additional 3/4 turn.
CAUTION
Never
overfill
crankcase.
Fill
only
to
maximum level as Indicated on dipstick.
13) Fill engine thru oil filler on top of engine
with 8.4 qt of lubricating oil. Use SAE
15W40 that meets Military 8pecifica- ton
MIL-L-2104
(API
CD
for
normal
temperatures. When temperature in the
voids consistently exceeds 1200F, use
SAE 40.
14) Start engine and run at idle for 5 minutes.
Turn off engine.
15) Check crankcase oil on dipstick and add
oil if necessary to bring to maximum
mark on stick Check for leaks around
filter. Tighten by hand, if necessary.
C-35
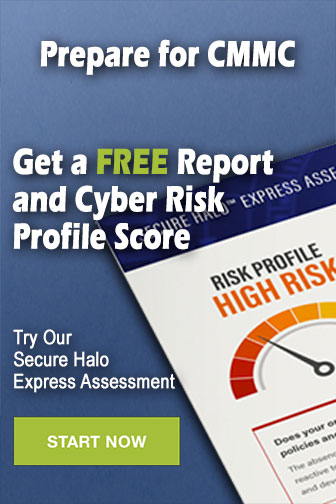