TM 55-2090-201-14&P
1-13.
OIL-WATER SEPARATOR OPERATING PRINCIPLES (Continued).
Air displaced by the rising fluid is discharged
through the air eliminator valve mounted on the
cover of the vessel.
When enough oil has gathered in the vessel it
becomes visible in a sight glass mounted on the
vessel.
A hand operated water discharge valve located at
the second stage outlet is closed during oil dis-
charge.
This provides the back pressure needed to
force oil from the top of the prefilter primary
separator.
Oil is discharged from the prefilter by
opening a hand operated oil discharge valve.
After the oil has been removed, the oil
discharge valve is closed and the water
discharge valve is opened.
Fluid in the bottom of the first stage then
enters the second stage separator.
Fluid flows up through the filter coalescer
element.
This filters any oil that may not
have been removed in the first stage.
Operation and function of the second stage
separator is the same as that of the first
stage.
(4) Controls for the type C and D separators are on a
remote control panel.
The panel contains a supply pump switch and
a monitor switch for future use.
Indicator lights show whether the
switches are on or off.
Also mounted on the control panel are
three pressure gauges.
These gauges read O-100 pounds per square
inch (psi).
One gauge shows the pressure at the inlet to the
prefilter primary separator.
The other two gauges show the pres-
sure at the discharge side of each Stage.
(5) The Pressure vessels are made of carbon steel. Each
vessel has a cam bar secured cover.
placed by removing this cover.
Filter elements may be re-
An air eliminator valve on each
unit vents air out of the separator as fluid enters.
Zinc anodes
in the bottom of each vessel cut down the effects of electrolysis
on the tanks.
1-23
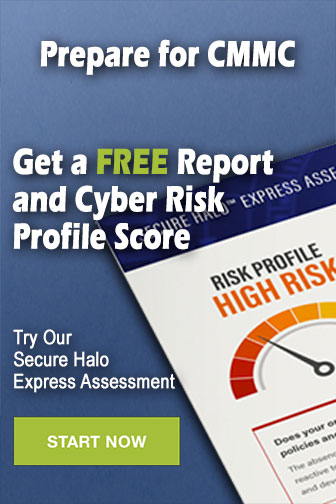