1-13. OIL-WATER
TM 55-2090-201-14&P
(6) Sight glasses on each unit show the oil level and
water clarity.
Elbows into which each of the sight glasses is
fitted are self-sealing.
This prevents leakage if a sight glass
breaks.
(7) Each separator has a combination water sample/drain
valve.
This permits draining each vessel or drawing samples if
needed.
(8) Both separators have a manual oil discharge valve.
(9) Three manual shut-off valves are located in the
system flow lines.
One is at the inlet to the first stage.
The
second is between the first and second stages.
The third is at the
outlet of the second stage.
This permits isolation of each stage.
(10) A flow rate gauge is installed in the water outlet
line.
b.
Type A and B Separators.
(1) The design of the A and B oil-water separator is based
on the principle of coalescence.
In this process oily water is pumped
through special filters.
Small droplets of non-soluble oil mixed in
the water attach to the filter surface.
There they combine (coalesce)
with other oil droplets.
When the oil drops become large enough, they
are forced off of the filter by fluid flow.
Due to the difference in
weight (specific gravity), oil separates from the water and rises to
the top.
(2) The unit has three separate vessels or stages. They
are connected in series.
The fluid (influent) containing oil, water
and solids is pumped to the system by a supply pump.
(3) The pump is equipped with a pressure relief valve.
This prevents the system back pressure from exceeding 45 psi (3163.8
gm sq cm).
(4) Primary separation and removal of oil from water takes
place in the first stage in the prefilter primary separator. Inside
the vessel is a replacable prefilter element.
Fluid flows from inside
to outside of the element.
It works as follows:
Fluid is pumped through the hollow core of the
filter.
1-24
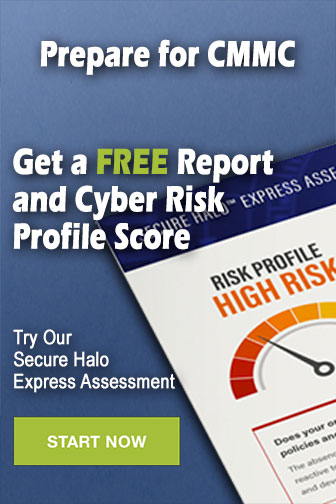