TM 9-4940-342-14&P
Table 5-1. Troubleshooting - Continued
Malfunction
Probable Causes
Corrective Action
4. Inadequate water supply, low
water pressure switch open (needs
15 psig to close) (refer to
malfunction 1). - Continued
m. Pump belt loose.
m. Inspect belt for tightness, if belt
can be twisted 2/3 of a turn tighten
by adjusting motor and oil pump in
slots in mounting base.
5. Excess temperature switch open
(outlet temperature exceeds 370°F).
a. Improper thermostat setting (too
high).
a. Observe outlet temperature gage,
Switch opens at 370°F. Lower
thermostat
to
desired
operating
temperature
and
manually
reset
switch.
b. Insufficient amount of water
flowing through coil.
b. See malfunction 4.
c. Switch setting incorrect.
c. Observe dial set point adjustment.
Switch should be set after operating
unit at high fire condition for ap-
proximately ½-hour. Set point to
trip burner at 370°F.
d. Switch not reset after high outlet
temperature condition (may occur
after coil blowdown).
d. Manually reset switch.
6. Low oil pressure switch open,
inadequate fuel supply pressure
(closes at 45 psi at thermostat
a. Improper thermostat setting (too
low or closed).
a. Observe position of thermostat and
open
(turn
counterclockwise
to
open).
outlet).
b. Fuel on-off supply closed (pump
discharge valve).
b. Observe valve position and open.
c. Fuel pump suction strainer valve
closed.
c. Zero pressure on pump discharge
gage. Open the valve.
d. Fuel strainer dirty.
d. Zero or low pressure on pump
discharge
gage.
Shut
strainer
suction valve. Clean or replace
strainer.
e. Oil pump rotation incorrect.
e. Observe motor rotation. Should be
clockwise when viewed from front
(pulley end) of motor. Correct
rotation by reversing any two of the
three 3-phase power leads.
f. Sensing connection for fuel pressure
switch plugged.
f. Remove ¼-inch copper tubing from
switch and connection at high fire
valve and turn on oil pump. Observe
oil flow from connection at valve.
Inspect for foreign material and
clean from the connection at high fire
valve. Blow the ¼-inch tubing
capillary out with air.
g. Fuel tank empty.
g. Oil pressure discharge gage will
drop in pressure trying to ignite low
fire burner. Refill tank.
h. Fuel pump recirculating by-pass
adjusted improperly.
h. Oil discharge pressure gage in-
dicates low or high pressure (should
be set 110-120 psi). With pump
running, remove protective cap from
adjusting screw. Insert screwdriver
and turn clockwise to increase
pressure and counterclockwise to
decrease pressure.
i. Fuel lines leaking, broken or
plugged.
i. Inspect piping for crimps, breaks or
leaks and repair or replace as
necessary. Disconnect oil supply
piping to fuel valves, turn on pump,
observe oil flow. Continue procedure
on oil tubing connections from valve
to pump until the plugged section is
located, and blow clear with air or
replace as necessary.
30
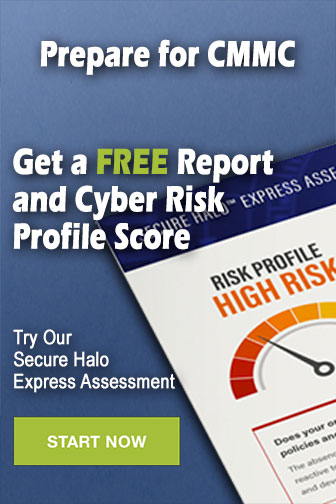