TM 9-4940-342-14&P
(5) With water recirculating, add inhibited
descaling acid at the rate of one pint every five
minutes. If badly scaled, every ten minutes until at
least three gallons have been added. Allow acid
solution to recirculate at least three hours.
(6) Test acid solution for strength periodically,
or if foaming subsides. A pinch of ordinary baking
soda will foam when dropped into active acid
solution. Keep recirculating active acid solution until
all foaming from gun discharge ceases and/or scale
chips no longer appear on filter screen.
(7) When descaling operation is completed, a
pump descale tank dry and flush entire system with
clear water for a full five minutes. Detach auxiliary
acid pump system and reconnect cleaner's water pump
to air dome inlet piping.
(8) Clean pump intake filter screen.
(9) To put cleaner back into operation, starting
procedure described in Chapter 2.
NOTE
It is recommended the water pump be cleaned and
inspected after the descaling operation. See water
pump servicing instruction.
5-7.
Checking Ignition Transformer (Refer to Fig
C-13)
a. Check for adequate spark by momentarily short
circuiting the transformer. Using a screwdriver
(insulated handle), touch transformer terminals, a ¾-
inch spark should be obtained. If no spark or less than
½-inch spark and power is available at transformer
primary, the transformer secondary is defective and
should be replaced.
b. Check burner assembly for possible high
voltage leaks in the electrode insulators. If in doubt,
replace electrodes.
5-8.
Flame Safeguard Control (Refer to Fig C-13
and Para 4-26)
a. Test the flame safeguard control as follows:
(1) Obtain a 20,000 ohm per volt DC volt-meter.
(2) Set the voltmeter on the 10 volt DC scale.
(3) Remove the cover by loosening the retaining
screw.
(4) Insert the probes until they come in contact
with the test jack (refer to fig 4-2 for location).
(5) The voltage signal will be as follows:
No flame present.................................... 0 voltages
Relay pull-in .......................................... 2 volts DC
Normal ................................................... 4 volts DC
Maximum .............................................. 5 volts DC
(6) Replace cover.
(7) With steam cleaner operating, remove UV
scanner from sight tube and cover scanner lens.
Flame safeguard control should shutdown unit and
positive fuel cutoff when the fuel valve is de-
energized.
b. Clean relay contacts using a burnishing tool or
fine crocus cloth, never a file or sandpaper.
5-9.
Belt Adjustment, Motor to Solution Pump
(Refer to Fig C-7)
a. The water pump, motor assembly is mounted on
a slotted base and need not be removed for belt
tightening or replacement.
b. To adjust V-belt, proceed as follows:
(1) With unit in an OFF position, disconnect
main power supply to cleaner.
(2) Inspect slot adjustment available on pump
mounting base and if adequate, loosen pump
mounting bolts and adjust pump to proper 2/3 twist
for proper belt tension. If proper adjustment is not
available, proceed as follows:
(a) Remove rear access panel by removing
four fastening screws.
(b) Loosen fuel pump mounting bolts and
relieve belt tension.
(c) Loosen the four bolts and nuts supporting
motor to base.
(d) Slide motor back until belt has proper
tension, normally 2/3 twist when tight. Inspect motor
and pump pulleys for proper alignment and secure
mounting bolts and nuts.
(e) Slide fuel pump back until belt has proper
tension, normally 2/3 twist when tight. Inspect fuel
pump, motor and blower pulleys for proper alignment
and secure mounting bolts and nuts.
(f) Replace rear access panel and turn on
main power to steam cleaner.
5-10. Low Oil Pressure Switch Adjustment (Refer
to Fig C-13)
a. With oil pump operating, fuel on-off valve
closed, take a reading on fuel pump discharge gage
and set to proper requirements, 110-120 psi.
b. Turn oil pump off, remove fuel pressure gage.
Install on outlet of thermostat control valve tee and
insert pipe plug in fuel pump gage port.
c. Start unit, open on-off valve, turn on low fire
start switch and ignite burner. Permit discharge
temperature to reach 325°F as indicated on outlet
temperature gage. As burner modulates on and off,
note pressure burner cuts out and in as indicated on
fuel oil pressure test gage.
d. Set cut-in on pressure switch (right hand screw)
by turning screw clockwise to raise pressure setting,
counterclockwise to decrease pressure setting. Switch
must be adjusted so burner ignition is achieved when
fuel pressure is between 50 psi to 60 psi.
e. Set cutout on pressure switch (left hand
34
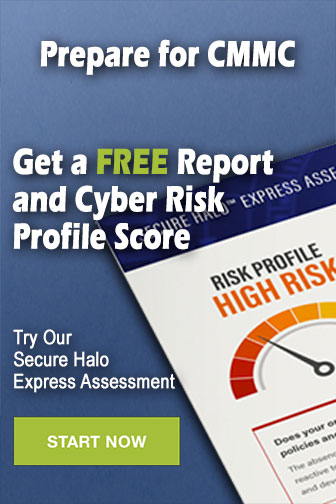