TM 9-4940-342-14&P
parts are reassembled in the exact former position.
6-3.
Motor Assembly (Refer to Fig C-10)
a. The motor should be inspected and defective
components replaced.
b. To repair the motor proceed as follows:
(1) Remove pulley setscrew(s) and slide
pulley clear from motor shaft.
(2) Remove motor electrical box cover, tag
electrical wires for proper reinstallation and
proceed to remove electrical wire nuts.
(3) Remove electrical cable connector nut
located inside of motor of motor junction box.
(4) Inspect motor components and replace as
required.
6-4.
Fuel Pump Repair (Refer to Fig C-12)
a. The fuel pump is designed to give years of
trouble-free service with minimum maintenance,
providing that only clean filtered kerosine, fuel oils
or diesel are used and fuel is kept free of water.
Never attempt to use gasoline or solvents of any
type or fuels containing gasoline, drain oils or
solvents. Avoid operating fuel pump without fuel in
supply tank.
b. Fuel pump is equipped with a two-pipe
system, fuel supply line and fuel return line, which
provides self-priming and air purging oil fuel
system. Keep both lines open, clean and free of any
leaks.
(1) The fuel pump is factory set to operate at
100-125 psi on fuel pressure service gage. Any
appreciable collapse of pressure indicates excessive
by-pass at by-pass plug, missing or damaged valve
gasket, worn piston assembly seal or worn gear set.
(2) The fuel pump has a cut-off valve
designed to stop all oil flow to fuel nozzles when
pump pressure drops below approximately 85
pounds. This prevents fuel dribble at nozzle during
shutdown or startup. If unit smokes during fire ON
or OFF operation, cutoff valve could be leaking. To
check, temporarily remove fuel pressure gage and
plug pressure gage port. Remove tube fittings to
burner nozzle and install fuel pressure gage in its
place. Operate fuel pump in ON position at pump
motor switch, then shut switch OFF. The gage
should hold approximately 85 psi or more. If
pressure drops below the cut-off point the valve
assembly should be disassembled, cleaned or
replaced, if necessary.
c. If seal leakage is suspected, the seal
assembly may be disassembled by removing the
three 10-24 screws from retainer ring, lifting off
retainer,
seal
spring
and
removing
seal
diaphragm. If required, the drive shaft, gear set
and thrustwasher can be removed for inspection or
replacement.
d. Before reassembly, dry the seal chamber
above the shoulder in the pump body. To make sure
there is some end play in shaft after reassembly,
pull on the shaft. Also make sure that the tab on the
thrustwasher mates with either seal drain hole in
pump body prior to reassembly of seal.
e. The fuel pump is equipped with an internal
filter and it should not be necessary to clean or
service it until five or six months after unit is in
service. This is due to the effective self-cleaning
action of the rotary filter.
f. To inspect or clean filter, remove filter cover
by removing the six 10-24 screws. Carefully pry
cover off, taking care not to damage the front cover
gasket. Wipe inside of cover clean, if necessary and
replace.
6-5.
Flame Safeguard, Scanner and Relay
Maintenance (Refer to Para 4-26)
a. With all external limit switches to flame
safeguard relay satisfied, terminals of the relay will
be powered in the following sequences.
(1) Terminal no. 7 of the flame safeguard
control will be powered through limit control
circuit no. 3.
(2). Flame safeguard terminal no. 8 is powered
through LS-1 (lockout switch). If LS-1 is open, the
flame safeguard requires a manual reset.
(3) Terminal no. 8, in turn, powers terminal
no. 6 and flame safeguard transformer T1.
(4) With T1 transformer powered, the time
delay network is energized through the LS heater
and contact RF-2 initiating the seven-second
prepurge timing.
(5) After completion of the seven-second
purge, the TD (time delay) relay is energized and
contact TD-1 closes, locking in the TD relay.
(6) Contact TD-2 also closes, energizing
terminal no. 3 and terminal no. 4 through contact
RF-3. Contact TD-3 opens.
(7) Terminal no. 3 powers circuit no. 7 to
open the low fire fuel valve. At the same time,
terminal no. 4 powers circuit no. 4 to power the
ignition transformer, producing the spark to ignite
the fuel.
(8) When the fire has been established and
detected by the UV flame detector, a signal will be
transmitted to the flame detector network through
terminals S1 and S2.
(9) The flame signal is amplified in the flame
detection network and flame relay (RF) is
energized.
47
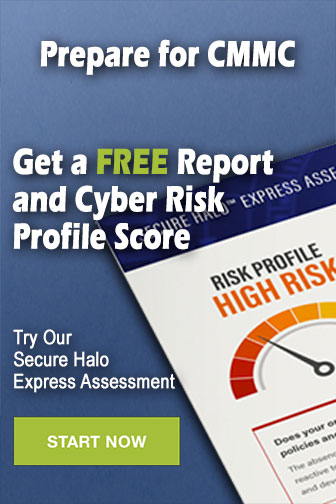