TM 9-4940-342-14&P
(10) When the RF relay is energized, contact
RF-2 opens and the LS heater circuit is
disconnected. Contact RF-3 opens and the ignition
transformer is de-energized. Contact RF-4 closes
and powers terminal 5.
(11) With terminal 5 energized, burner switch
high may be closed, powering the high fire fuel
valve through control circuit no. 6.
(12) In the event flame is not detected within
12 seconds after TD relay is energized, the LS
heater will trip the lockout switch opening LS-1,
which disconnects power to terminal 8, all load
terminals and TD-2. LS-2 closes and terminal A
(alarm) is energized. The flame failure light is
powered through control circuit no. 8. Before
restart, the lockout switch (red reset button) will
have to be reset.
(13) In the event of flame failure, fuel is
interrupted within two seconds. Ignition is not
brought back on until after a new seven-second
prepurge cycle. If the low fire flame fails to
reignite, lockout will occur in 12 seconds.
(14) In the event that the flame relay is
energized (flame detected) at any time during the
prepurge, RF-1 will close and by-pass the time
delay network, bringing it back to 0 seconds, where
the timing stops until the flame relay is de-
energized.
(15) If the flame relay should remain in an
energized position, RF-5 will be closed and the LS
heater will be powered through RF-5 and TD-3.
Lockout will occur in 12 seconds.
(16) If, during normal operating conditions,
any of the limit switches open, terminal no. 7 will
be de-energized. The TD relay will de-energized
and contact TD-2 will open, closing the fuel valves.
After condition which opened the limit switch is
rectified, a new seven-second prepurge is required
before the low fire fuel solenoid valve and ignition
transformer is powered.
NOTE
During normal modulation of the burner, the fuel
low pressure switch will open causing recycling of
the burner.
(17) If the above sequences do not occur in
the manner listed and the difficulty has been
isolated to the UV scanner and relay, first test for
continuity across the scanner leads. If scanner
shows open, replace scanner.
(18) If scanner is functional, inspect relay for
mechanically bound flame relay or time delay relay
(refer to fig 4-2). Inspect relay contact blocks and
observe if blocks are cocked on guides. Free
contact block and assure block moves contact
freely.
(19) Inspect
relay
for
broken
or
loose
conductors, broken solder joints or broken or loose
terminals. Repair as necessary.
(20) If difficulty cannot be isolated by the
preceding steps, the relay should be replaced.
6-6.
Coil Inlet Assembly (Refer to Fig C-14)
All fittings and components should be inspected and
replaced if found to be defective. No attempts shall
be made to patch, plug, solder or weld leaking
fittings.
6-7.
Burner Plate Assembly (Refer to Fig C-16)
The burner plate weld assembly may be repaired
when utilizing normal welding procedures for equal
or similar components. Plate assembly shall require
removal of all components prior to welding or other
major
repairs.
Major
damage
is
cause
for
replacement.
6-8.
Outlet Coil Assembly (Refer to Fig C-17)
All fittings and components should be inspected and
replaced if found defective. For replacement of
valves only, these fittings requiring removal shall be
disassembled
from
assembly.
Always
start
disassembly sequence at component being repaired to
minimize fitting removal. No attempts shall be made
to patch, plug, solder or weld leaking fittings for
distort fittings for forced installation.
6-9.
Outlet Assembly Soap Tank (Refer to Fig C-
31)
A defective valve is cause for rejection and no
attempts to repair it shall be made.
6-10. Air Dome Outlet Assembly (Refer to Fig C-
25)
All fittings should be inspected for defects and
replaced if found defective.
6-11. Wheel Assembly Blower (Refer to Fig C-26)
The wheel assembly blower may be disassembled for
component part replacement only. No attempts shall
be made to weld, peen or patch blower plate casting.
Blower cage is not repairable and must be replaced if
inspection reveals defects.
6-12. Switch Assembly and Breaker (refer to Fig
C-28)
a. Remove magnetic starter contact block and
inspect contacts for cleanliness. If contacts have
carbon deposits, clean with burnishing tool or fine
crocus cloth.
b. Remove magnetic coil, test continuity across
coil. If coil shows open, replace.
c. Check ratchet wheels on thermal overload
48
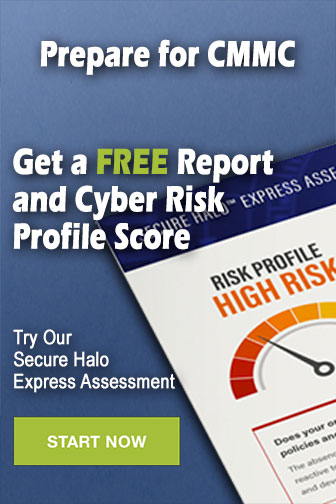