TM 10-6630-246-12&P
TM 09241B-12&P
Section III. OPERATOR PREVENTIVE MAINTENANCE CHECKS AND
SERVICES (PMCS)
2-7.
GENERAL.
Preventive Maintenance Checks and Services means systematic caring, inspection, and servicing of
equipment to keep it in good condition and ready to use. As the operator, your mission is to:
(1)
Be sure to perform your PMCS each time you use the Water Quality Analysis Set: Purification.
(2)
Do your "Before" PMCS just before you use the equipment.
(3)
Do your "After" PMCS right after using the equipment.
(4)
Use DA Form 2404 (Equipment Inspection and Maintenance Worksheet) to record any faults that you
discover before, during, or after use, unless you can fix the fault. You DO NOT need to record faults that you fix.
2-8.
PMCS PROCEDURES.
a.
Your Preventive Maintenance Checks and Services, table 2-1, lists inspections and care required to keep the
equipment in good operating condition.
b.
The "Interval" column of table 2-1 tells you when to do a certain check or service.
c.
The "Procedure" column of table 2-1 tells you how to do required checks and services.
NOTE
Terms "ready/available" and "mission capable" refer to same status: Equipment is on hand and ready to
perform its mission. (See DA Pam 738-750.)
d.
The "Equipment Is Not Ready/Available If:" column in table 2-1 tells you when your equipment is non mission
capable and why it cannot be used.
e.
If the equipment does not perform as required, notify supervisor.
f.
If anything looks wrong and you cant fix it, write it on your DA Form 2404 IMMEDIATELY, report it to your
supervisor.
g.
When you check for "operating condition", you look at the component to see if it is serviceable.
2-5
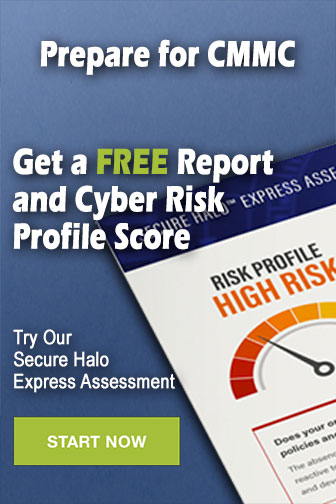