TM 55-1930-209-14&P-1
12-8 Prestart procedures. Prestart procedures include before operation checks and procedures.
12-8.1 Startup after extended shutdown. Refer to paragraph 12-10.2 for extended shutdown information.
a.
Check system components for loose wires. Make sure fittings are tight, gauges are dean and have intact glass
faces. Check pipes for leaks. Repair or replace as necessary.
b.
Check oil level in sight glass on compressor as follows:
(1)
Barge 1 (Figure 12-4). Oil should be visible in lower half of sight glass. If oil cannot be seen in sight glass,
remove oil cover nut in center of air intake assembly. Carefully pour not more than one pint of oil into oil
tube. Do not spill oil onto air filter assembly. Continue to add oil one pint at a time until oil level is between
bottom and halfway mark on sight glass. Do not overfill. Use only non-detergent oil, SAE 10W, API
classification CD or SF, or MIL-L-2104 or MIL-L-46152.
CAUTION
On Barges 2 and 3 air compressors, NEVER allow oil level to fall more than 1/8
Inch below full level mark on sight glass.
(2)
Barges 2 and 3, (Figure 12-5). Oil should be up to full level mark on sight glass. If not, unscrew oil plug to
left of sight glass and add a non-detergent, rust and oxidation inhibiting industrial oil with viscosity
equivalent to an SAE grade 20 weight motor oil. See page 5, Form 5S 1408, Operating and Service Guide
for Dayton Speedaire Models, for recommended oils by brand name and designation. Add oil until it
reaches full level mark on sight glass. DO NOT OVERFILL. Replace oil filler plug.
c.
Close compressed air main supply valve on forward end of receiver by turning handle at right angle to pipe.
d.
Drain air filters 1 and 2 by opening drain valves on bottom of filters (Figure 12-7). When water and moisture have
drained, close drain valves.
WARNING
When bleeding pressure from air compressor drain cock ALWAYS use protective
shield to protect eyes and face from flying particles. Wear gloves and avoid skin
damage by closing buttons and collars and by rolling down shirt sleeves on work
clothing.
e.
Drain receiver by turning drain cock clockwise (small T-handle) on bottom of tank (Figures 12-4 and 12-5). When
draining is complete, dose valve.
f.
Turn adjusting screw on bottom of pressure regulators 1 and 2 counterclockwise until screw turns freely (Figure
12-6).
g.
Check that air station valves 1 thru 9 are dosed.
h.
Make sure switchboard circuit breaker P5 is dosed (ON) to provide power to power panel 1.
i.
Make sure power panel 1 circuit breaker 3P5 is dosed (ON) to provide power to air compressor electric controller.
j.
Turn controller AUTO MANUAL switch to MANUAL (Figure 12-3).
12-10
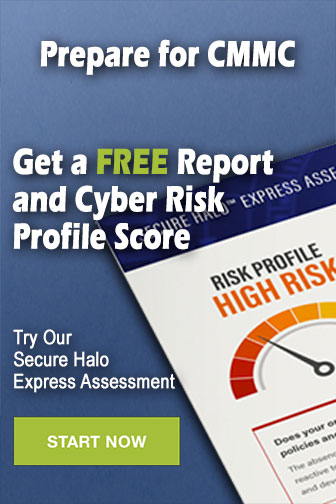