CHAPTER IV
SEC III CONT. · SEC IV · SEC. V
CONTROL THERMOSTAT
2.
WATER REGULATING VALVE
The water regulating valve is sensitive to water line
pressure. Under normal conditions adjustable valves
require only an initial adjustment. Water regulating
valves of the self-adjusting type need no adjustment, but
erratic operation may be found when water pressures
are sub-normal or above normal. When water pressures
exceed 80 PSI, a water pressure regulator should be
installed in the water supply line ahead of the cooler and
adjusted to 40 PSI.
SECTION IV - FIELD REPLACEABLE PARTS
The parts listed below should be field replaced.
WATER REGULATING VALVE
Turn off water supply and relieve the water pressure.
Remove water regulating valve and replace. Due to the
variety of water regulating valve s, specific instructions
regarding a valve can be had on request. Please give
model, style, and serial number information found on
Model Plate with this request.
STRAINER - DRAIN
Unscrew or snap strainer from drain.
CABINET TOP AND SIDE PANELS
Remove and replace as explained in Chapter II, Section
m.
TEMPERATURE CONTROL
The controlling thermostat is mounted in the machinery
compartment. Disconnect the power supply
and detach thermostat. Remove power element from
bulb well on cooling unit.
FAN AND MOTOR ASSEMBLY
Turn off electrical supply. Remove fan and motor
'assembly. NOTE - Handle fan blade with care. Mis-
alignment can cause noise and/or motor failure.
COMPRESSOR
OVERLOAD
PROTECTOR
AND
RELAY
Disconnect power supply and remove compressor
terminal cover. Replace relay and overload with exact
factory replacement.
COMPRESSOR CAPACITOR
Remove and replace with factory replacement.
CONDENSER WATER REGULATING VALVE
Turn
off
water
supply
and
replace
with
factory
replacement unit.
SECTION V - AUTHORIZED REPAIR STATION
The hermetic refrigeration system of a cooler in warranty
must never be opened in the field. Such repair work
should be done at an authorized repair station.
If warranty has expired, the components of the
refrigeration system can be field replaced. Extreme
care has to be taken in cleanliness, dehydration,
evacuation and charging of the system. Cleanliness is
most important in servicing the system, since dirt can
contaminate or cause a restricted flow of refrigerant
through the system.
Maximum care is maintained in the production of
the cooler to assure a moisture level of 10 PPM or less.
Moisture cannot be tolerated in the system, since it has
an oxidizing effect on the refrigeration parts or may
freeze the capillary exit blocking the flow of the
refrigerant.
Precautions are also taken in manufacture to
exclude air and non-condensibles from the system.
The system is swept with a refrigerant vapor and
evacuated to 250 microns.
Charging of the system with refrigerant is critical.
An overcharge causes the suction line to frost or sweat
and may cause damage to the compressor.
The service man attempting to service the
refrigeration system in the field should have a vacuum
pump capable of pumping down to 100 microns, a
vacuum gauge capable of reading 10 microns, a
Halogen leak detector capable of sensing a refrigerant
leak of 0.10 ounces per year, a charging system capable
of charging within 0. 10 ounces by weight and a
thorough knowledge of the refrigeration system.
It is highly recommended therefore, to have the
cooler with an internal refrigeration defect repaired at an
authorized repair station.
12
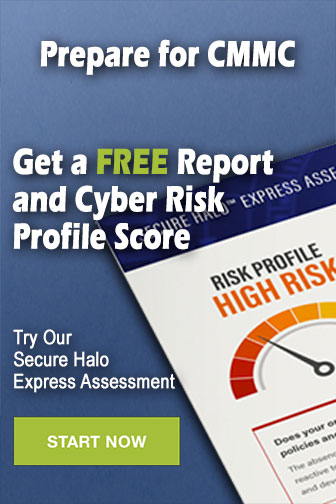