TM 55-1930-209-14&P-15
· Before welding on fuel oil or sludge tank, make sure tank is gas free by:
- Removing all liquid from the tank.
- Cleaning tank thoroughly.
- Seeing that tank is thoroughly dry.
- Force ventilating the tank.
· Never weld on submerged part of the hull.
· Always have a fire extinguisher handy when welding.
· Keep arc welding work cable connected as close to welding area as possible. Work cables connected to
barge framework or other locations far from welding area increase the possibility of welding current passing
through lifting chains, crane cables or other possible circuit paths. This can create fire hazards or overheat
lifting chains or cables until they fail.
· Never use compressed air or oxygen for purposes of ventilation.
· Always weld with all doors, portholes, and hatches propped open and all available ventilation systems
operating.
· Take frequent breaks away from area when welding.
· Always maintain all welding equipment in proper working condition. If you have any doubts about the safety
of any welding equipment, do not use the welder.
3-8.3.1 Operating procedures for arc welder
NOTE
Arc welder is NEMA-rated for a 30% duty cycle. Duty cycle Is based on a 10 minute
period. Therefore it can be operated at full output (250 amperes (Amps)) for 3
minutes out of each 10 minute period without overheating. At 50% duty cycle, the
output rating is 200 Amps.
a.
Perform prestart procedures according to paragraph 3-7.1.
b.
Start welder and check direction of rotation. Proper direction is shown by an arrow on the nameplate. Direction
of rotation can be changed by interchanging any two input leads. For two-phase, three-wire input power,
interchange two outside leads. Be sure neutral wire is connected to motor neutral, which is the center terminal on
the starter. For two-phase, four-wire input power, interchange two leads in the same phase.
c.
Use CONTINUOUS VOLTAGE CONTROL to adjust to desired voltage and to obtain exact current required for the
job. This control will also vary the open circuit voltage to adjust the arc characteristics to suit different welding
applications. The CONTINUOUS VOLTAGE CONTROL dial is divided into equal divisions marked 40 to 60 open
circuit volts. Generally, high open circuit voltage from 50 to 60 volts provides a steady, smooth and stable arc for
speedy downhand welding. Low open circuit voltage from 40 to 50 volts provides a digging type arc required for
overhead and vertical welding.
d.
Adjust current using CONTINUOUS CURRENT CONTROL dial to suit your particular welding needs.
CONTINUOUS CURRENT CONTROL has a single dial calibrated in Amperes. This control handle also has five
pointers corresponding to the five major divisions on the CONTINUOUS VOLTAGE CONTROL dial. When
CONTINUOUS VOLTAGE CONTROL dial is set on 55, for example, approximate welding current is indicated by
the pointer marked 55 on CONTINUOUS CURRENT CONTROL handle.
3-10
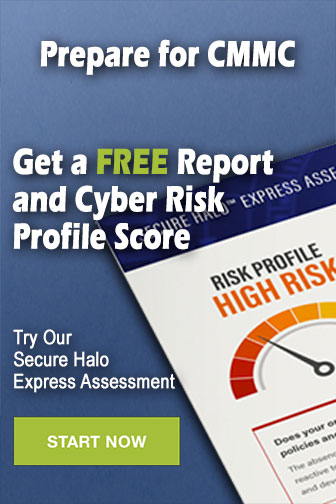