TM 55-1930-209-14&P-2
4-7.2.6.1 Cleaning and inspection
a.
Make sure ROWPU control station for pump being repaired is electrically dead by opening (OFF)
switchboard circuit breaker P6 for seawater pump 1 or P7 for seawater pump 2. Redtag circuit breaker
with: WARNING - DO NOT ACTIVATE. REPAIRS BEING MADE."
b.
Wipe clean exterior of control station with clean rag. Open control station door and vacuum clean or
clean inside with electrician's brush. Avoid using solvents for cleaning inside of control station. Solvents
leave a greasy film on components that may reduce electrical conductivity.
c.
Check fuse. Replace if necessary.
d.
Visually inspect for indications of burns, corrosion, loose connections, damaged parts, or chipped paint.
Clean corrosion from contacts and terminals, tighten loose connections, and replace damaged parts.
Clean electrical contacts with silver polish, fine sandpaper, or burnishing tool. DO NOT use emery paper
or emery cloth or steel wool. Vacuum to remove residue. Touch up paint according to TB 43-0144.
4-7.2.6.2 Test and repair
a.
With main circuit breaker P6 or P7 on switchboard closed (ON). Check control station input line voltage
across points L1 and L2, L2 and L3, and L1 and L3 (Figure 4-1). If voltage across any two points is 0,
power source is at fault. Go to step b to correct problem. If voltage across all three pairs of points is 440,
go to step c to check control station output voltage.
b.
Check circuit breaker P6 or P7 output line voltage. If voltage across any two lines is 0, circuit breaker or
power source is at fault. If circuit breaker voltage across all three line pairs is 440, replace power cable
from circuit breaker to control station.
c.
Check control station output line voltage across points T1 and T2, T2 and T3, and T1 and T3. If voltage
reading across any of the terminal pairs is 0, check motor controller thermal units using Figure 4-1 as
given in step d below. If voltage across all terminal pairs is 440, pump motor is at fault and check motor
as given in paragraph 4-7.2.1.
d.
Check voltage of overload protection thermal units across points K1 and K2, K2 and K3, and K1 and K3.
If voltage across any terminal pair is 0, replace faulty overload protection thermal unit. If voltage across
all terminal pairs is 440, go to step e.
e.
Check transformer output voltage from terminal board TB 12 to TB 19. If voltage is 110, go to step f. If
voltage reading is not 110, check continuity of fuse and wire from transformer to TB12 and wire from
transformer to TB19. Replace fuse or wire if at fault.
f.
Check transformer input voltage across points L1 and L2. If voltage is not 440, replace wires to
transformer. If voltage is 440 and voltage in step e was 0, replace transformer. If voltage is 440 and
voltage in step e was 110, go to step g
g.
Open (OFF) and secure main circuit breaker P6 or P7 on switchboard and check control station continuity
as follows:
(1)
Check continuity of ON/OFF/START switch in ON position from terminal board TB12 to TB6. If
check indicates a closed circuit, go to step (2). If check indicates an open circuit, check continuity
of wires from points P1 to TB6 and TB12 to P3. If check indicates an open circuit in wire, replace
faulty wire. If check indicates a closed circuit in both wires, replace faulty ON/OFF/START
switch.
(2)
Depress pump 1 or pump 2 local STOP switch and check continuity from TB14 to TB15. If check
indicates closed circuit, go to step (3). If check indicates an open circuit, check continuity of wires
from TB14 to S4 and TB 15 and S3. If check indicates an open circuit, replace faulty wires. If
check indicates a closed circuit in both wires, replace faulty STOP switch.
4-13
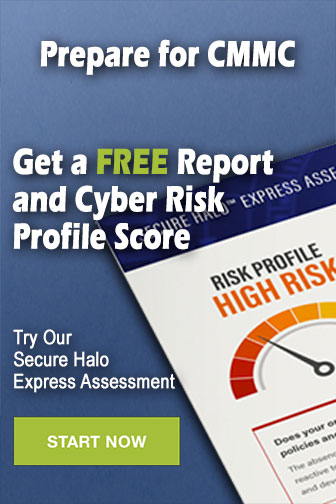