TM 55-1930-209-14&P-21
5 Turn cylinder head bottom side up.
6 Lubricate small end of reamer into injector tube.
7 Use a speed handle and remove excess stock at bottom end of tube. Ream until small end of
tube is flush to .005 inch below finished surface of cylinder head.
(e) Ream bevel seat in injector tube as follows:
1 To determine amount of metal to be removed from bevel seat, place injector gage into injector
tube. Zero dial indicator to fire deck. Dial injector should be flush, i .014 inch with fire deck (Figure 6-19).
2 Install injector in tube and note relationship between surface of spray tip and fire deck of
cylinder head as shown in Figure 6-19. This will determine amount of stock that must be reamed from bevel seat in tube.
CAUTION
Wear safety goggles when using compressed air.
3 Wash interior of injector tube with fuel oil and dry thoroughly with compressed air.
4 Place a few drops of cutting oil on bevel seat of injector tube. Carefully lower reamer into tube
until it contacts bevel seat.
5 Without applying any downward force, make a trial cut by turning reamer steadily. Remove
reamer, blow out chips and note what portion of bevel seat has been cut.
6 Proceed carefully with reaming operation, withdrawing the reamer occasionally to observe
progress.
7 Remove chips from injector tube and using an injector for a gage, continue reaming operation
until shoulder of spray tip is either flush or extends a maximum of 0.015 inch below fire deck or cylinder head as
illustrated in figure 6-19.
(6) Push Rods and Cam Followers (Cylinder Head Removed)
(a) Install pushrod spring retainers (Figure 6-18) in cylinder head.
(b) Install lower spring seat, spring, and upper spring seat on pushrod. Then, install assembled
pushrod into cylinder head in proper bore.
(c) Screw pushrod locknut on each pushrod as far as possible; then, screw the pushrod into rocket arm
clevis until end of rod is flush with or above inner side of clevis.
(d) Immerse cam followers in a screen type basket and place basket in a container of lightweight
engine oil (heated to 100° to 125°F) for at least 1 hour before installation. Rotate cam follower rollers during soaking
period to aid in purging any air from bushing roller area.
6-39
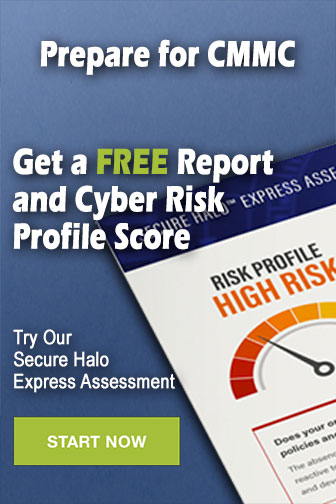