manifold (18) and manifold plate (17) for cracks,
surface scoring, brinelling or spalling. Replace
manifold or manifold plate that exhibits any of
these conditions. A polished pattern on the
ground surfaces from commutator or rotor
rotation is normal.
8.
Remove rotor set (16) and wear plate (15), by
again using the two bolts as a lifting tool. Retain
rotor set in its assembled form, if possible, to
maintain the same rotor vane to stator contact
surfaces. Inspect the rotor set in its assembled
form for nicks, scoring, or spalling, on any
surface and broken or worn rotor splines. If any
rotor set component requires replacement, the
complete rotor set must be replaced as it is a
matched set. Inspect the wear plate for cracks,
brinelling, or scoring.
9.
Place rotor set on a flat surface and center rotor
(16A) in stator (16C) such that two rotor lobes
(180° apart) and a roller vane (16B) centerline
are on the same stator centerline. Check the
rotor lobe to roller vane clearance with a feeler
gage at this common centerline. If there is
more than .005 inches (0.13 mm) of clearance,
replace rotor set.
10.
Remove drive link (14) from coupling shaft (11)
if it was not removed with rotor set and wear
plate. Inspect drivelink for cracks and for worn
or damaged splines. No perceptible lash (play)
should be noted between mating spline parts.
11.
Remove thrust bearing (13) and inspect for
wear,
brinelling,
corrosion,
and
a
full
complement of retained rollers.
12.
Remove coupling shaft (11) by pushing on the
output end of shaft. Inspect coupling shaft
bearing and seal surfaces for spalling, nicks,
grooves,
severe
wear
or
corrosion
and
discoloration. Inspect for damaged or worn
internal
and
external
splines
or
keyway.
Replace coupling shaft if any of these conditions
exist.
NOTE: Minor shaft wear in seal area is
permissible. If wear exceeds .020 inches
(0.51 mm) diametrically, replace coupling
shaft.
A slight "polish" is permissible in the shaft
bearing area. Anything more would require
coupling shaft replacement.
13.
Remove sleeve (22) by inserting screwdriver
between sleeve and housing (6) and pry up.
Inspect sleeve for deformation from the original
cylindrical shape to a "barrel" or "hour glass"
shape. Inspect sleeve ends for severe nicks,
burrs or corrosion. Replace sleeve if any of
these conditions exist.
NOTE: Minor burrs and corrosion that would
damage new seal rings during assembly can
be removed from sleeve ends.
14.
Remove seal ring (7) from housing (6) and
discard seal ring.
15.
Remove housing (6) from vise, turn over and
reclamp in vise with dirt seal (1) end pointed up.
16.
Remove dirt seal (1), retaining .ring (2), back-up
washer (3), washer (4), and seal (5) from
housing (6). Discard seals and washers but
keep retaining ring(2) for comparison when
selecting new retaining ring from seal kit. If burr
exists on retaining ring groove, remove with a
scraping tool.
17.
Inspect housing (6) assembly for cracks, the
machined surfaces for nicks, burrs, brinelling or
corrosion. Remove burrs that can be removed
without changing dimensional characteristics.
Inspect tapped holes for thread damage. If the
housing is defective in these areas, discard the
housing assembly and the disassembly of the
Torqmotor is complete.
18.
If the housing assembly (6) has passed
inspection to this point, inspect the bearings (9),
(10), (12) and thrust washers (8) and (8A). The
bearing rollers must be firmly retained in the
bearing cages, but must rotate and orbit freely.
All rollers and the thrust washers must be free of
brinelling and corrosion. If the housing has
passed this inspection the disassembly of the
Torqmotor is completed.
19.
If
only
the
outer
bearing
(12)
requires
replacement, carefully use a suitable bearing
puller to remove bearing so the housing is not
damaged.
20.
If bearing (10) requires replacement, use a
1.488 inch (37.80 mm) maximum diameter shaft
or a 1.745 inch (44.32 mm) maximum diameter
shaft based on the internal seal (5) bore
diameter and press out thrust washers (8), (8A),
thrust bearing (9), and bearings (10) and (12).
The housing wearplate face should be placed on
a block of wood during the pressing operation to
protect it. Discard thrust washers (8) and (8A),
thrust bearings (9), and bearings (10) and (12)
and replace with new parts, as parts will have
been damaged when being pressed out.
NOTE: The depth or location of bearings (10)
and (12) in relation to the housing wearplate
face should be measured and noted before
pressing the bearings out. This will
facilitate the correct reassembly of new
bearings.
The disassembly of Torqmotor is completed.
7
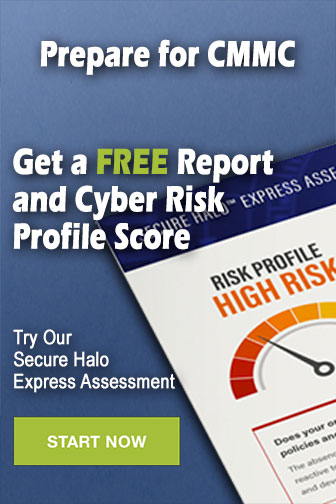