TORQMOTOR ASSEMBLY PROCEDURES
(Reference Exploded Assembly View)
Replace all seals and seal rings with new ones each time you
reassemble the Torqmotor unit. Lubricate all seals and seal
rings with SAE 10W40 oil or clean grease before assembly.
NOTE
Individual seals and seal rings as well as
a complete seal kit are available. The
parts should be available through most
OEM parts distributors or Ross approved
Torqmotor distributors. (Contact your
local dealer for availability.)
NOTE
Unless otherwise indicated, do not oil or
grease parts before assembly.
Wash all parts in clean petroleum-based
solvents before assembly. Blow them
dry with compressed air. Remove any
paint chips from mating surfaces of the
end cover, sleeve, and housing and from
port and sealing areas.
HOUSING BEARING REPLACEMENT PROCEDURES
1.
If
bearing
components
were
removed
for
replacement, assemble new thrust washer (8), new
thrust bearing (9) and new thrust washer (8A) in that
order into housing 161 bearing cavity. If thrust
washer (8A) has a chamfer on the inside diameter,
the chamfered side must face away from thrust
bearing (9).
NOTE
Thrust washer (8A) will be identical to
thrust washer (8) unless a chamfered
inside diameter is required because of
coupling shaft design.
NOTE:
An appropriate size piloted bearing
mandrel is required to press in housing
bearings.
2.
If bearings (10) and (12) required are for a 2.25 inch
(57.2 mm)l diameter (nominal) housing bearing bore,
press in new bearing (10) which is 1.0 inch (25.4
mm) long, into housing 161 bearing bore to a depth
of 2.410 ± .010 inch (61.2 ± 0.254 mm), measured
from the housing wear plate contact surface . Then,
press in new bearing (12) which is .5 inch (12.7 mm)
long into housing bearing bore to a depth of .115 ±
.010 inch (2.92 ± 0.254 mm) measured from the
housing wear plate contact surface.
NOTE
Press against the lettered end of bearing
cage when pressing in a roller bearing
assembly.
3.
If the bearings (10) and (12) required are for a 2.50
inch (63.5 mm) diameter nominal) bearing bore,
press in new bearing (10) which is 1.0 inch (25.4
mm) long into housing 161 bearing bore to a depth of
2.379 ± .010 inch (60.43 ± 0.254 mm) measured
from housing wear plate contact surface . Press new
bearing (12) which is identical to bearing (10) into
housing bearing bore to a depth of .115 ± .010 inch
(2.92 ± 0.254 mm) measured from the housing wear
plate surface.
NOTE
The bearings (10) and (12) must be
assembled to the correct depths to
assure the necessary clearance for
thrust washer (8A) and thrust bearing
(13) and to assure required bearing
support.
TORQMOTOR ASSEMBLY.
If the sealing diameter of the coupling shaft (11) is larger than
any other diameter on the output end of the coupling shaft,
begin the Torqmotor assembly procedures with Step 1 below .
If there is a diameter on the output end of the coupling shaft
equal to the sealing diameter of the coupling shaft begin the
procedures with Step 6 below.
1.
Place housing (6) in a vise and clamp down on
housing port bosses with small bore end pointed up .
Apply clean grease to new seal (5) and assemble
into housing with seal lip pointed inward.
2.
Hold washer (4) between thumb and index finger and
slightly collapse to facilitate assembly into housing
(6).
3.
Assemble back-up washer (3) in to housing (6) with
the anti-rotation tab facing out.
4.
Select a new retaining ring (2) from the seal kit, that
is the same thickness as the retaining ring removed.
Assemble the new retaining ring into housing 16) .
Be sure rounded edge of retaining ring is faced
inward and that back-up washer tab is between ends
of retaining ring.
5.
Apply a small amount of clean grease to back side of
new seal (1) and assemble into housing (6), if a seal
Ill is required.
6.
Invert housing (6) in vise so that the large bore end is
up.
7.
Apply cellophane tape around splines or keyway on
coupling shaft (11) to prevent damaging seals.
8.
Assemble coupling shaft (11), firmly seating it
against thrust washer (8A).
9.
Assemble thrust bearing (13) onto end of coupling
shaft (11).
10.
Assemble drive link (14) into coupling shaft (11) with
their splines in mesh. (Align hole in drive link with
hole in coupling shaft (11), if applicable.)
NOTE
Two alignment studs screwed finger
tight
into
housing
(6)
boltholes,
approximately 180o apart, will facilitate
the
assembly
and
alignment
of
components as required in the following
procedures. The studs can be made by
cutting off the heads of 318-24 UNF 2A
bolts that are over .5 inch (12.7 mm)
longer than the bolts (24) used in the
Torqmotor.
11.
Assemble wear plate 1151 over drive link (14) and
studs onto housing (6).
12.
Install assembled rotor set (16) with counterbore in
rotor (16A) down, if applicable, and splines in mesh
with drive link splines.
NOTE
If necessary, go to "Rotor, Stator, Vane
Assembly" procedures on page 9.
13.
Assemble manifold plate (17), manifold (18) and then
the commutator ring (21) over the drive link (14) onto
rotor set (16) per the exploded assembly view. Be
sure swirls in manifold and manifold plate are faced
together.
8
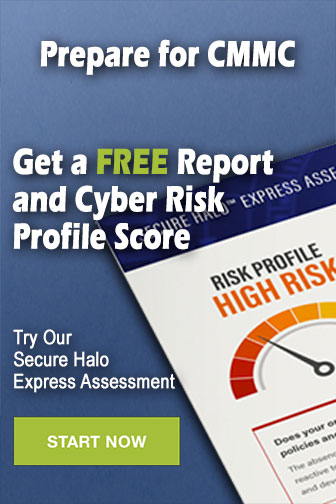