SERIES 3300 "OlLescer" OIL REMOVAL FILTER
PARTS LIST AND INSTRUCTION SHEET
INSTALLATION - Install filter units so the airflow is in the direction IN-
OUT as indicated on the head of all units. Filters should be installed
up-stream of regulators. If air dryer is being used, install the filter down
stream from the dryer. In most cases a pre-filter with a 10 micron
sintered bronze element or a cotton absorbent filter element is
recommended to greatly extend the life of the oilescer element. When
the oilescer element becomes clogged with dirt, it must be replaced. If
it is kept free from dirt, it will coalesce oil definitely. A pre-filter will
remove water and dirt before it reaches the oilescer and is less costly
to maintain. The oilescer filter is then free to remove oil, oil vapors,
and sub-micron sized particles without prematurely clogging with large
particles of dirt and scale. Normal operating maximums for plastic
bowls are 150 P.S.I. or 150F. Do not install filters with polycarbonate
bowls in the presence of materials on the list in these instructions. A
metal bowl must be used under these conditions. The use of a bowl
guard is recommended under all conditions.
Metal bowls are available for pressures up to 250 P.S.I.
WARNING - Units are die cast aluminum, do not over torque when
installing. Also, pressurize unit slowly after installation of unit or
new element to avoid damage to element.
MAINTENANCE - Accumulated oil and moisture should be drained off
by the petcock regularly. The Arrow model 5200 Float Drain can be
assembled in place of drain cock to automatically eject moisture and oil
at regular intervals. Collected oil should not be permitted to fill above
the lower baffle.
To replace element unscrew ringnut by hand - DO NOT USE
WRENCH. Remove bowl, and filter element wingnut. Then remove
baffle and expended element. Filter element should be replaced when
pressure drop exceeds 10 P.S.I. Filter bowls are to be cleaned only
with kerosene or soapy water. Inspect gaskets and O ring, replacing
any which are damaged or distorted. Tighten ringnut by hand, making
sure O ring seal is in filter head groove.
OPERATION ADJUSTMENTS - If the filter is installed properly, it
should give long trouble-free serviceable pressure drop across the filter
should not excess 10 P.S.I. If the pressure drop exceeds 10 P.S.I.,
either the filter element needs to be replace, or the unit is being
operated beyond its capacity, and a larger size unit is required.
Operating the filter at a pressure drop excess of 10 P.S.I. will greatly
reduce the efficiency of the filter.
If oil appears downstream; 1) check downstream air lines to be sure
that they are free of residual oil; 2) check to see that the filter element
gasket and "O" ring are in good condition and installed properly.
THE FOLLOWING MATERIALS
WILL HARM A POLYCARBONATE BOWL:
Acetaidhyde
Ethylene chlorohydride
Acetic acid (conc.)
Ethylene dichloride
Acetone
Formic acid (conc.)
Acrytonitrile
Freon (refrigerant & propellant)
Ammonium fluoride
Gasoline (high aromatic)
Ammonium sulfide
Hydrochloric acid (conc.)
Benzene
Methyl alcohol
Benzoic acid
Methylene chloride
Benzyl alcohol
Milk of lime (CaOH)
Bromobenzene
Nitric acid (conc.)
Butyric acid
Nitrobenzene
Carbolic acid
Nitrocellulose lacquer
Carbon disulfide
Phenol
carbon tetrachloride
Phosphorous hydroxy chloride
Caustic potash solution (5%)
Phosphorous trichloride
Caustic soda solution (5%)
Propionic acid
Chlorobenzene
Pyridine
Chloroform
Sodium sulfide
Cresol
Styrene
Cyclohexanol
Sulfuric acid (conc.)
Cyclohexanone
Sulphural chloride
Cyclohexene
Tannergas
Dimethyl formamide
Tetrahydronaphthalene
Dioxene
Thiophene
Ethane tetrachloride
Toluene
Ethyl ether
Xylene
Ethylamine
Never use a polycarbonate bowl on an application where:
1. Pressure exceeds 150 P.S.I.
2. The temperature range does not fall between 40F to 120F.
3. Air is supplied by a compressor that is lubricated with synthetic oils
or oils containing phosphate eaters or chlorinated hydrocarbons.
4. Polycarbonate plastic bowls are exposed to materials such as
carbon tetrachloride, trichlorethylene, acetone, paint thinner,
cleaning fluids, or other harmful materials.
5. Do not use with synthetic compressor oils or oils containing
aromatic hydrocarbons. A straight mineral bases oil is
recommended for the line lubricator.
If materials harmful to polycarbonate are present either outside or
inside the bowl or you do not meet its pressure or temperature
range, use either a metal bowl with sight glass or metal bowl.
ITEM
FILTER PARTS
PART NO. FOR MODEL-PIPE SIZE
NO.
NAME
2302-1/4
3302-1/4
3364-1/2
3306-3/4
3308-1
1
Polycarbonate bowl & Drain Cock
32017
33017
33017
36017
36178
2
Ring Nut (Bowl)
32023
32023
32023
36023
36023
3
Filter Head
32037
32038
34038
36038
38038
4
Filter Element Kit
23050
33050
33050
36050
38050
5
O Ring (Bowl)
2260
3340
3340
3460
3460
6
Rod/Element Screw
32060
33070
33070
36055
36055
7
O Ring (Rod)/Gasket
0070
32090
32090
0080
0080
8
Gasket/O Ring
0160
32080
32080
1300
1300
9
Metal Bowl Guard
32190
34190
34190
36190
-----
10*
Metal Bowl Adapter & Drain Cock
32174
33174
33174
36174
36174
11
Hex nut
-----
-----
-----
39043
39043
* Optional
** Metal Bowl
ARROW PNEUMATICS, INC.
P.O. Box 739 Mundelein, Illinois 60060
Fluid Power Division
Phone: (312) 566-9100
FORM 3300
2/81
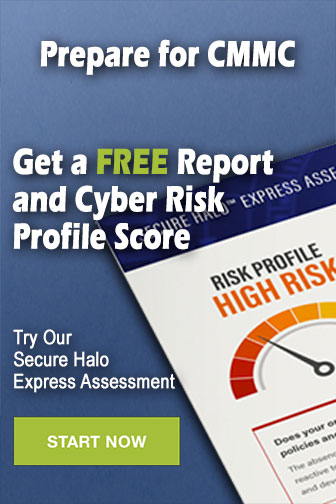