in burner volute supporting center section of
heater shell to frame assembly.
(8) Using a forklift or crane, lift preheat coil
assembly from chassis being careful not to destroy
gasket located between heater shell and frame.
b. Installation. For ease of installation it is
advisable to position front of heater shell in proper
relative position to location on frame prior to
lifting. To install proceed as follows:
(1) Using a forklift or crane, raise heater
shell and install gasket over mounting bolts. (If
lifting attachments are unsafe, gasket may be
placed on chassis mounting plate before heater
shell assembly mounting bolts are lowered through
gasket holes.)
(2) Lower heater shell onto chassis mounting
plate and guide mounting bolts through plate
holes.
(3) Install and secure the three 3/8-inch nuts
and six ½-inch nuts supporting heater shell to
chassis assembly.
(4) Reverse procedures in paragraph 5-18a,
steps (1) through (8) for preheat coil removal.
5-19. Hourmeter (Refer to Fig 2-1)
a. Removal. The hourmeter may be removed
without the need of instrument panel disassembly.
To remove hourmeter proceed as follows:
(1) Disconnect main power supply to unit
and turn all switches OFF.
(2) Remove the four screws mounting the
electrical junction box located on back side of
panel.
(3) Disconnect the electrical wires from
hourmeter to power source by removing wire nuts
and separating wires.
(4) Remove the three hourmeter mounting
screws, nuts, lockwashers, while supporting
hourmeter in location.
(5) Gently remove hourmeter from panel in
forward motion using care not to snag electrical
wires.
b. Installation. Reverse the procedures in
paragraph 5-19a, steps (1) through (5).
5-20. Soap Tank Outlet Assembly (Refer to Fig
C-23)
a. Removal. Should the soap control valve
assembly need repairs and require removal,
proceed as follows:
(1) Remove valve handles on those valves
which may interfere with instrument panel when
swinging away from unit.
(2) Remove the four instrument panel
mounting screws and swing panel away from unit
exposing soap control valve assembly.
(3) Drain soap tank of all liquids and remove
check valve cap on soap intake check valve to
main water pump.
(4) Loosen clamp and remove hose assembly
at soap control valve connection.
(5) Unscrew soap control valve assembly
from soap tank mounting nipple.
b. Installation. To install soap control valve
assembly reverse procedures in paragraph 5-20a,
steps (1) through (5).
5-21. Air Dome Outlet Assembly (Refer to Fig
C-25)
a. Removal. The air dome outlet plumbing
assembly may be removed without disturbing the
air dome location. To remove proceed as follows:
(1) Remove clamps and spuds from pump to
air dome hose assembly and from air dome to coil
inlet assembly where connected to air dome
plumbing.
(2) Unscrew air dome plumbing assembly
from air dome chamber.
b. Installation. To install outlet assembly
reverse procedure in paragraph 5-21a, steps (1)
and (2) and seal all joints with teflon tape or pipe
dope.
5-22. Air Dome (Refer to Fig C-4)
a. Removal. When air dome removal is
required follow procedures in paragraph 5-21a,
steps (1) and (2) and proceed as follows:
(1) Disconnect copper tube line located on
top of air dome vent assembly.
(2) Remove the two 3/8-inch nuts, washers
and one ¼ -20 nut, washer and screw on mounting
brackets.
(3) Gently lift air dome until air dome outlet
coupling clears hole in chassis mounting plate.
b. Installation. To install air dome reverse
procedures in paragraph 5-22a, steps (1) through
(3) and use teflon tape or pipe dope on all pipe
connections.
5-23. Wheel Assembly Blower (Refer to Fig C-
26)
a. Removal. The wheel assembly blower
consists of a blower cage, blower bearing and
blower bearing case assembly, all of which must
be removed as a unit. For removal proceed as
follows:
(1) Remove clamp and hose from water
pump to air dome assembly at air dome.
Reposition hose spud or air dome assembly to
permit clearance of blower case assembly.
TM 9-4940-342-14&P
37
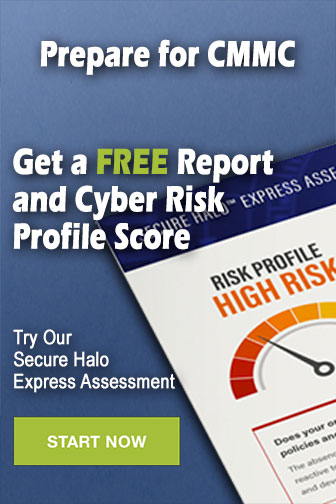