TM 9-4940-342-14&P
(2) Loosen fuel pump mounting bolts and
relieve belt tension then remove belt from blower
pulley.
(3) Remove three ¼ -20 hex nuts and washers
securing blower mounting plate to blower housing
and gently remove blower assembly from housing.
Blower assembly must be removed by guiding
blower cage clean of housing clearance hole.
NOTE
Blower cages are balanced for concentric operation
and must not be bumped, dropped or subjected to
any unusual pressure.
b. Installation. To install blower assembly,
reverse procedures in paragraph 5-23a, steps (1)
through (3) and proceed as follows:
(1) Adjust blower belt in accordance with
paragraph 4-22.
5-24. Blower Cage (Squirrel) (Refer to Fig C-26)
a. Removal. The blower cage need not be
removed for tightening of cage to blower bearing.
Cage setscrew may be secured by removing air gate
plate and intake screen allowing entrance to cage
assembly from outside of unit. If removal is
required proceed as follows:
CAUTION
Unit electrical power must be disconnected and all
switches in the OFF position.
(1) Follow procedures in paragraph 5-23a,
steps (1) through (3).
(2) Loosen blower cage setscrew located in
hub and slip cage clear of bearing shaft.
b. Installation. To install blower cage on bearing
shaft reverse procedure in paragraph 5-24a, step (2)
and
proceed
with
wheel
assembly
blower
installation, paragraph 5-23b.
5-25. Blower Bearing (Refer to Fig C-26)
a. Removal. To remove the blower bearing
follow procedures in paragraph 5-24a, steps (1) and
(2) and proceed as follows:
(1) Remove blower drive pulley on bearing
shaft.
(2) Remove snapring retaining bearing within
blower case plate.
(3) Press out old bearing by placing flat
surface (hub up) of casting on flat surface of arbor
press allowing clearance for bearing to be removed.
If press is not available, bearing may be removed by
tapping on end of gearing shaft with block of wood
or brass mallet.
b. Installation. To install blower bearing reverse
procedures in paragraph 5-25a, steps (1) through
(3). Long end of bearing shaft must be
inserted into blower casting first to achieve proper
extension for mounting of drive pulley.
5-26. Oil Tank Drain Assembly (Refer to Fig C-
30)
a. Removal. Should repairs or replacements be
necessary on the oil tank drain assembly proceed as
follows:
(1) Drain all fuel from fuel tank.
(2) Unscrew drain valve and related plumbing
from tank.
(3) Remove hose spud fitting from valve
outlet.
b. Installation. To install oil tank drain assembly
reverse procedures in paragraph 5-26a, steps (1)
through (3).
5-27. Soap Tank Overflow Assembly (Refer to
Fig C-4)
a. Removal. To remove the overflow assembly
proceed as follows:
(1) Remove overflow nipple support clamp,
overflow hose clamps and unscrew assembly in
counterclockwise direction.
(2) Valve replacement may be accomplished
by removing inlet and outlet fittings.
b. Installation. To install overflow assembly
reverse procedures in paragraph 5-27a, steps (1)
and (2) and seal all joints with teflon tape or pipe
dope.
5-28. Air Dome Vent (Refer to Fig C-32)
a. Removal. To remove the air dome, vent
disconnect copper tube line and unscrew valve or
assembly.
b. Installation. To reinstall, tighten fittings and
connect copper tubing.
5-29. Oil and Soap Tank (Refer to Fig C-4)
a. Removal. Should oil and soap tank removal
be necessary observe the following procedures:
(1) Remove valve handles on valves which
may interfere with opening of instrument panel and
remove four mounting screws on panel right side.
(2) Swing panel away from unit and remove
soap control valve assembly, clamp, nipple and
elbows on top of soap tank, fuel fill spout assembly,
overflow soap tank assembly, fuel drain assembly
and fuel filter assembly.
(3) Remove fuel pump bypass hose and clamp
at fuel tank connection.
(4) Remove
nuts,
washers
and
bracket
securing air dome to soap tank.
(5) Remove seven nuts securing tank to
chassis mounting plate.
(6) Using a forklift or crane, lift tank from
38
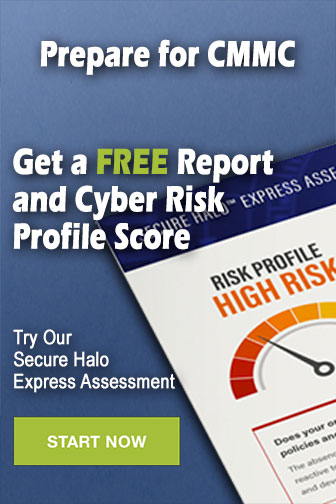