T M 1 0 - 4 6 1 0 - 2 3 2 - 12
Table 4-2. Unit Troubleshooting Guide (Continued)
MALFUNCTION
TEST OR INSPECTION
CORRECTIVE ACTION
2.
3.
8.
Step 4. Remove connector P24 from the switch panel. Check continuity across J24A and J24D.
If the continuity check is okay, replace the cable between P11 and P24 (Reference Interconnection
Diagram FO-2 , Sheet 14) (para. 4-27).
High pressure pump high pressure light or horn doesnt work (Reference Schematic Diagram FO-1, Sheet 9,
schematic lines 903-904 and Schematic Diagram FO-1, sheet 10, schematic line 1011). Refer to light testing
and alarm troubleshooting for additional test procedures.
Notify direct support maintenance.
High pressure pump high pressure alarm on at less than 900 psig (6205 kPa), or, is not on and system pressure
is more than 960 psig (6619 kPa).
Notify direct support maintenance.
Product high pressure switch does not work (Reference Interconnection Diagram FO-1, Sheet 9, schematic
lines 905-906).
Step 1. Check operation of switch. Refer to unit PMCS for procedure.
If switch is not working, go to step 2.
Step 2. Shut down the ROWPU. Remove connectors P12 and P11 from the control panel. Check for 110-120
VAC across J11A and J12J.
If voltage is not present, notify direct support maintenance.
Step 3. Check continuity across P11A and P11E.
If the continuity check is okay, notify direct support maintenance.
Step 4. Remove connector J24 from the switch panel. Check continuity across J24A and J24E (Reference
Interconnection Diagram FO-2, Sheet 14).
If the continuity check is okay, replace the cable betweenP11 and P24 (para. 4-27).
Product high pressure light or horn does not work (Reference Interconnection Diagram FO-1, Sheet 9, sche-
matic lines 906-907 and 1012).
Refer to light testing and alarm troubleshooting for additional test procedures.
Notify direct support maintenance.
Product high pressure alarm is on and product pressure is less than 35 psig (241 kPa) or alarm is not on and
pressure is higher than 45 psig (310 kPa).
Notify direct support maintenance.
Strainer high differential switch does not work (Reference Interconnection Diagram FO-1, Sheet 9, schematic
lines 908-909).
Step 1. Shutdown the ROWPU. Remove connectors P12 and P11 from the control panel. Check for 110-120
VAC across J11A and J12J.
If voltage is not present, notify direct support maintenance.
Step 2. Check continuity acrossP11A and P11F.
If the continuity check is okay, notify direct support maintenance.
Step 3. Remove connectors P24 from the switch panel. Check continuity across J24A and J24F. If the conti-
nuity check is okay, replace the cable between P11 and P24 (para. 4-27).
Strainer high differential light or horn does not work (Reference Schematic Diagram FO-1, Sheet 9, schematic
lines 909-910, and Schematic Diagram FO-1, Sheet 10, schematic line 1006).
Refer to light testing and alarm troubleshooting for additional test procedures.
Notify direct support maintenance.
Strainer plugged Iight is on and basket strainer is clean or light is not on and strainer is plugged.
Notify direct support maintenance.
Media filter high differential switch does not work (Reference Schematic Diagram FO-1, Sheet 9, schematic
lines 911-912).
Step 1. Check operation of switch. Refer to unit PMCS for procedure.
If the switch is not working, go to step 2.
Step 2. Shutdown the ROWPU. Remove connectors P12 and P11 from the control panel. Check for 110-120
VAC across J11A and J12J.
If voltage is not present, notify direct support maintenance.
9.
10.
4-44 Change 1
5.
6 .
7.
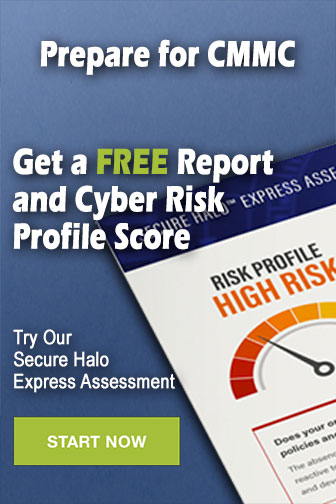