TM 10-4610-232-34
Table 2-1. Direct Support Troubleshooting Guide (Continued)
MALFUNCTION
TEST OR INSPECTION
CORRECTIVE ACTION
5. Air storage tank suspected of holding water.
WARNING
Extreme care must be used in the following procedure. If the pressurized air tank is
dropped, damaging the valve, the tank could possibly swing violently and cause
personal injury or equipment damage.
Run the air compressor and build up 50 psig air pressure. Turn the air compressor off and close the air storage
tank valve. Relieve the air system pressure by opening a drain valve on either air manifold. Disconnect the air line
to the air storage tank and, carefully, remove with the air tank from its mounts (para. 2-60). Hold the tank vertical
with the valve on the bottom and slowly open the valve. If there is any water in the tank, it will be blown out.
If there is water in the tank, troubleshoot the outlet air filter for bypassing water.
6. Air pressure cycles rapidly between 1500-1800 psig.
Step 1. Check air blowdown solenoid valve for internal leakage. Remove the outlet tubing from the solenoid valve
and feel if air is leaking through the valve when it is supposed to be closed. Disconnect the valve electrical
connector if air can be felt leaking.
(a) If air leaks through the valve at all times, clean/repair the air blowdown solenoid valve (para.
2-51).
(b) If the air leak stops when the electrical connector is disconnected, refer to air blowdown solenoid
valve electrical troubleshooting and unit troubleshooting.
Step 2. Shut the ROWPU down and turn off the air compressor. Relieve all air system pressure and then close
the air storage tank valve. Start the air compressor and let the air pressure build to 1800 psig. Open the
air tank block valve. A rush of air should be heard as the air tank valve is opened and the tank starts filling.
(a) If there is no sound the air tank inlet is plugged. Check air lines at the tank for plugging.
(b) If there is a sound like air bubbles in the tank, refer to water in air tank troubleshooting.
Step 3. Check for air leaks or a device that is using too much air if the above steps have not revealed the problem.
Somewhere air is being consumed as fast as the air compressor puts it out.
(a) Check by process of elimination and repair all air system leaks.
(b) Replace the air tank if the above steps have not corrected the problem (para. 2-60).
7. Outlet air filter filled with a white, oily substance.
Step 1. The substance is an oil/water mixture that comes from the air compressor.
Disassemble the filter chamber assembly and clean it out (para. 2-59).
Step 2. Check the outlet filter air blowdown solenoid valve for plugging.
Disassemble the air blowdown solenoid and clean it out (para. 2-51).
Step 3. Check the outlet filter blowdown solenoid valve for correct operation. Start the air compressor and check
that the solenoid valve opens and blows down an air/water mixture for about 30 seconds every 15
minutes of compressor operating time.
(a) If the valve does not operate correctly, refer to air blowdown valve electrical troubleshooting and
unit troubleshooting.
(b) Replace/repair the air blowdown valve if troubleshooting indicates the valve is non-operational
(para. 2-51).
2-6
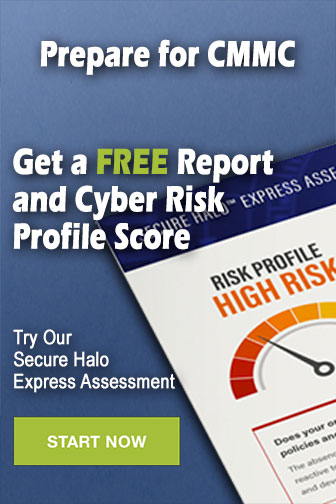