TM 10-4610-232-34
Table 2-1. Direct Support Troubleshooting Guide (Continued)
MALFUNCTION
TEST OR INSPECTION
CORRECTIVE ACTION
2. Air compressor does not turn over easily by hand.
Visually confirm malfunction.
Send air compressor to General Support Maintenance for overhaul.
3. Air compressor motor is noisy.
Turn motor shaft by hand. It should turn easily, without noise, without dragging, and without rough spots.
(a) Replace bearings if rotation is not smooth (para. 2-72).
(b) Replace motor if teardown inspection reveals worn or damaged rotor or stator (para. 2-71 ).
4. Air compressor has localized overheating.
Locate which cylinder is overheating as recompression or high cylinder pressure is causing the problem.
Replace the inlet and outlet valves on the affected chamber (para. 2-72).
5. Air compressor is noisy.
Identify noise.
NOTE
Light tapping when compressor is started is normal.
(a) Continuous light tapping is caused by the oil dipstick. Remove it and make sure it is straight.
(b) Light knocking is probably a small-end bearing. Replace air compressor and send it to General
Support Maintenance for repair (para. 2-72).
(c) A rumbling noise in the main bearings. Replace the air compressor and send to General Support
Maintenance for repair (para. 2-72).
6. Air compressor interstate relief valves keep blowing.
Locate which relief valve is blowing as this generally indicates pressure leaking back or rising cylinder pressure on the
following stage.
(a) Replace the leaking interstage relief valve (para. 2-72).
(b) Replace the inlet and outlet valves on the following stage (para. 2-72).
(c) Replace the air compressor and send it to General Support Maintenance for repair (para. 2-72).
7.
Air compressor runs but does not build up pressure.
Step 1. Close the air tank block valve and operate the air compressor.
(a) If the pressure goes up to compressor shutdown point, the air compressor is working correctly. Check
for leaks downstream of the air regulator.
(b) If the pressure does not rise to compressor shutdown-check for leaks or plugging upstream of the
pressure regulator.
Step 2. Check all relief valves for leakage. If any are leaking, check for plugging of air lines (especially in freezing
conditions) which might be causing the valve to relieve.
If no cause can be found for the valve leak, replace the leaking relief valve. (Interstate and high pressure
relief, para. 2-70). (Low pressure relief, para. 2-61.)
Step 3. Check air blowdown solenoid valve for internal leakage. Remove the outlet tubing from the solenoid valve
and feel if air is leaking through the valve when it is supposed to be closed. Disconnect the valve electrical
connector if air can be felt leaking.
(a) If air leaks through the valve at all times, clean/repair the air blowdown solenoid valve (para. 2-51).
(b) If the air leak stops when the electrical connector is disconnected, refer to air blowdown solenoid
valve electrical troubleshooting and also unit level troubleshooting.
Step 4. Check the relief valve on the back of the air pressure regulator.
If it is leaking, replace the regulator (para. 2-61).
2-4
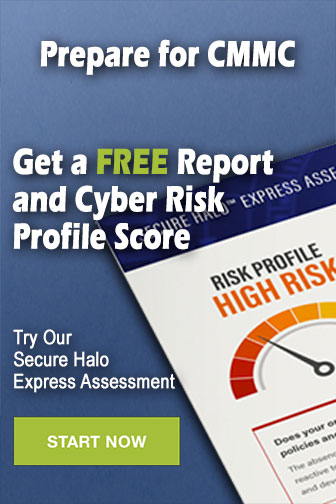