BOOSTER PUMP
CYCLONE SEPARATORS
TM 10-4610-232-34
Table 2-1. Direct Support Troubleshooting Guide (Continued)
MALFUNCTION
TEST OR INSPECTION
CORRECTIVE ACTION
8.
Air compressor runs continually. (Also, see air compressor runs but does not gel to 1700 psig, malfunction 8).
Step 1.
Shut the ROWPU down. Close each valve on both air manifolds, one at a time, and note if the closing of a valve
allows the air compressor to build up pressure. If a particular valve closing allows the air compressor to build
up pressure, troubleshoot that line, its fittings, and the components in that line for leakage. Remove tubing
from the outlet side of solenoid valves to check for leakage through the valve if the leakage is traced to one of
them.
Replace/repair low pressure air components that are found to be leaking.
Step 2.
Notify Direct Support/General Support to check high pressure valves and fittings for leaks.
Replace/repair high pressure valves, fitting and components that are found to be leaking.
(MODEL WTA-060 ONLY)
No flow through the separators.
Check for internal plugging.
Disassemble separator and remove blockage, replace cyclone liners if damaged (para. 2-14).
1.
Booster pump assembly Is noisy.
Step 7.
Check for foreign objects in pump.
Disassemble pump (para. 2-39).
Step 2.
Inspect pump internals for wear and damage.
Replace worn or damaged parts (para. 2-39).
Step 3.
Turn the motor shaft by hand. It should turn easily, without noise, without dragging, and without rough spots.
If rotation is not smooth, bearings are bad. Replace motor bearings (para. 2-40).
2
Booster pump does not supply sufficient pressure or flow.
Check pump internals for wear and damage.
Replace worn or damaged parts (para. 2-39).
3.
Booster pump motor hums but will not turn.
Step 1.
Check for foreign objects in pump.
Disassemble pump (para. 2-39).
Step 2.
Inspect pump internals for wear and damage.
Replace worn or damaged parts (para. 2-39).
Step 3.
Tag and disconnect motor leads (T1, T2, T3) (REF: Interconnection diagram FO-2, Sheet 10). Set multimeter
to Ohms x 1000 scale and connect test leads between each motor lead and the motor frame. Readings should
be infinity for each step.
Replace motor if the meter reading is zero (para. 2-40).
Step 4.
Set multimeter to Ohms x 1 scale and check for continuity between all pairs of motor leads, T1 and T2, T1 and
T3, T2 and T3. Readings should be zero or near zero for each step.
Replace motor if reading is infinity (para. 2-40).
Step 5.
Turn the motor shaft by hand. It should turn easily without noise, without dragging, and without rough spots.
If rotation is not smooth, bearings are bad. Replace motor bearings (para. 2-40).
Change 3 2-7
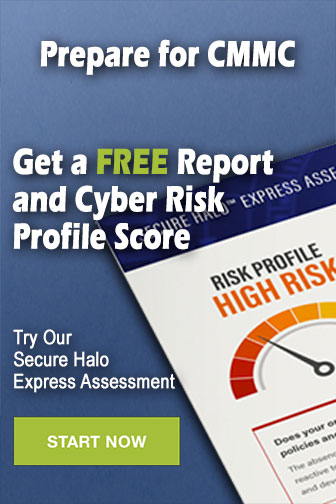