TM 55-1930-209-14&P-1
3-19.3 Prestart procedures
a.
In ROWPU space, make sure EMS is operating by pushing up on monitor controller left of monitoring processor.
If monitor does not come on, turn it on with switch beneath the screen. For more details on EMS, see
TM 55-1930-209-14 & P-11.
b.
Check maintenance records to make sure all required maintenance checks and services have been completed.
c.
In void 4, conduct walk-around inspection of generator set to detect visible deficiencies that, if not corrected, could
become hazardous to people or equipment.
WARNING
At operating temperatures, engine coolant is hot and under pressure. It also
contains alkaline materials harmful to eyes and skin. To avoid personal Injury,
check coolant level only when engine Is stopped and filler cap is cool enough to be
touched with a bare hand. Should engine coolant come in contact with eyes or
skin, Immediately flush affected area with clean water and seek medical assistance
if necessary.
CAUTION
Sensing element must be submerged In coolant to operate. If coolant Is low,
engine can overheat and automatic shutoff will not function to prevent damage to
engine.
d.
When engine is cool, slowly open coolant tank filler cap. Check that engine coolant is not more than 1/2 inch
below top of filler pipe. If it is, fill to required level with clean fresh water (low in scale-forming minerals but not
softened water) and cooling system conditioner. Always add conditioner to water. Never use plain water.
Conditioner should be 3 percent by volume of total coolant capacity - about 1/2 pint of conditioner per 2 gallons of
water. If cap gasket is tom or damaged, repair or replace gasket.
e.
Check that crankcase oil shows between ADD and FULL marks on dipstick. If oil shows below ADD mark, add oil
at oil fill, located above oil dipstick on accessory end of engine. Oil must meet engine service classification CD
(MIL-L-2104) or CD/TO-2. Diesel engines onboard use 15W40 as standard crankcase lubricant for normal
temperatures. If temperatures in voids consistently exceed 1200F, use SAE 40.
f.
Check that batteries are dean of corrosion, all cable connections tight and covered with anti-corrosion grease, and
electrolyte covers plates.
g.
Check that fuel pressure gauge indicates NORMAL. If gauge indicates CAUTION or OUT, wash primary fuel filter
and replace secondary fuel filter element. (See TM 55-1930-209-14 & P-9, for details.)
h.
Drain water and sediment from fuel/water separator (if SSG is so equipped).
i.
Check that engine has fuel oil (for further information on fuel oil system, see TM 55-1930-209-14&P-8) by setting
fuel oil valves as follows:
(1)
For SSG 1: Close fuel oil valves FO13-FO15, FO17, FO18, FO20, FO21, FO24-FO27, and open fuel valves
FO16, FO19, and FO23.
(2)
For SSG 2: Close fuel oil valves FO13-FO16, FO18, FO20, FO21, FO23, FO25-FO27 and open FO17,
FO19, and FO24.
j.
Check that 24 Vdc power panel in workshop is active (Figure 3-18) and circuit breaker 8P14 is dosed (ON). This
action provides voltage to hold open solenoids in generator fuel lines. Emergency shutdown switches activate
these shutoff solenoids by removing this 24 Vdc power. If 24 Vdc panel is not active and circuit breaker 8P14 is
open (OFF), these holding solenoids are dosed and fuel for these generators is shut off. The generator will start
and run for about 2 minutes until lack of fuel shuts it off.
3-39
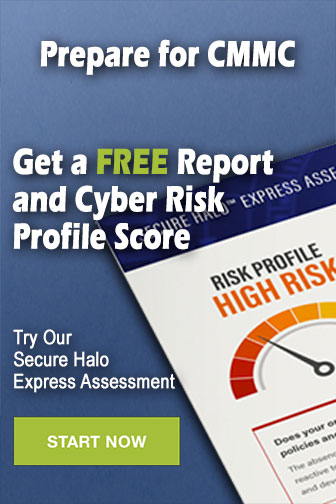