it is possible to obtain the exact current you require. Also. by means
of this control. you can vary the open circuit voltage to adjust the arc
characteristics to suit different welding applications.
The Continuous Voltage Control dial is divided into equal divisions
marked 40 to 60 open circuit volts. Generally the high open circuit
voltage from 50 to 60 volts provides a steady. smooth and stable arc
desirable for speedy downhand welding. The low open circuit voltage
from 50 to 40 volts provides a digging type arc required for overhead
and vertical welding.
How to Set the Controls
Example: Assume you want to make a vertical up weld using a 5/32
electrode at about 135 amps. A snappy digging arc (medium low open
circuit voltage) is required to give the best control of the arc in the
whipping technique that must be used.
1. Set the Continuous Voltage Control to about 45.
2. Set the Continuous Current Control to read 135 amperes under the
pointer marked 45.
3. Strike the arc
4. If the arc is too weak, turn the Voltage control up for higher voltage
and higher current If a still higher current is required. turn the
Current Control up 10 or 20 amperes. In the final adjustment be
certain the Voltage control is still set for the lower part of the scale
to provide the snappy arc recommended for vertical welding.
LINCONTROL® (Accessory)
The Lincontrol is a foot operated current control for welding light gage
material. All "Aircraft" models are equipped with the required wiring to
operate with the Lincontrol. All other models can easily be adapted for
operating with the Lincontrol by installing a receptacle (S-7588-1) and
a special rheostat (M-5090-K). Write for IM-113-A for further
information.
MAINTENANCE
WARNING: Have qualified personnel do the maintenance work and trouble shooting. Turn the
input power off using the disconnect switch at the fuse box before working inside the machine.
BEARINGS
Your welder is equipped with double-shielded ball bearings having
sufficient grease to last indefinitely under normal conditions. Where
the welder is used constantly or in excessively dirty locations. it may
be necessary to add one ounce of grease per year to the bottom
bearing and one half ounce to the top bearing.
When greasing the bearings, use a good grade of bearing grease.
Keep all dirt out of the area. Wipe the fittings clean and use clean
grease and equipment. More failures are caused by dirt introduced
during greasing than from insufficient grease.
When replacing the bearings check the bearing cage for excessive
wear.
COMMUTATOR AND BRUSHES
The generator brushes are properly adjusted when the welder is
shipped They require no particular attention DO NOT SHIFT THE
BRUSHES or adjust the rocker setting
Periodically inspect the commutators and brushes by removing the
commutator covers. DO NOT remove or replace these covers while
the machine is running.
Commutators require little attention. However, if they are black or
appear uneven, have an experienced maintenance man clean them
with fine sand paper or a commutator stone. Never use emery cloth or
paper for this purpose.
Replace brushes when they wear within 1/4" of the pigtail. A complete
set of replacement brushes should be kept on hand. Lincoln brushes
have a curved face to fit the commutator. Seat these brushes by lightly
stoning the commutator as the armature rotates at full speed until
contact is made across the full face of the brushes After stoning blow
out the dust with low pressure air
WARNING: Uncovered rotating equipment can be dangerous.
Use care so your hands, hair, clothing or tools do not catch in the
rotating parts. Protect yourself from particles that may be thrown
out by the rotating armature when stoning the commutator.
PREVENTIVE MAINTENANCE
1. Turn the welder off at the fuse box before doing work inside the
machine. See page 2 for additional safety precautions
2. Blow out the welder and controls with an air hole once every two
months. In particularly dirty location, this cleaning may be
necessary every week. Use low pressure air to avoid driving dirt
into the insulation.
3. Inspect the starter every six months. Brush any accumulation of
dust out of the starter.
4. Rotate the Current Control through its entire range twice each
morning This cleans the contacts to lessen the possibility of the
contact "freezing". Do not do this while welding.
5. Keep electrode and work connections tight.
-4-
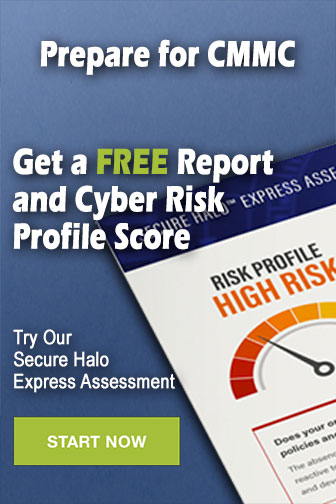