TROUBLE SHOOTING
WARNING: Have maintenance personnel do the maintenance work and trouble shooting. Turn the
input power off using disconnect switch at the fuse box before working inside the machine.
TROUBLE
CAUSES
WHAT TO DO
Machine fails to start.
Power circuit may be dead.
Look for open switch, fuses removed from clips or blown
Power circuit may be single phased.
Look for one blown fuse or one dead line.
Machine may be jammed.
See that armature turns over easily by hand, and look for
foreign material in air gap.
Overload heater links may be tripped.
When machine has had time to cool press start button to
reset links and to start the welder.
Power line voltage not suitable for the
Check line voltage and make sure it agrees with nameplate
motor, or input voltage too low.
voltage. If voltage is too low have power company check
for line losses.
Motor trips off the line.
Power circuit may be single phased.
Check for one blown fuse or dead line.
Welder may be operating above current
Check load against nameplate.
capacity.
Welding leads may be too long or too small.
See Table on page 3.
in cross-section.
Ventilation may be impaired.
Make sure that the space under dome is open and that the
louvers in base are clear of any obstructions that would
interfere with normal ventilation of the machine.
Motor input voltage too low.
Motor supply voltages should not fall below 90% of normal
voltage. Have power company check transformer and line
capacity. If supply lines are too long or too small they should
be corrected. (Se Table on page 3.)
Welder may be connected for 460V and
Check the connection for proper voltage.
running on 230V.
Welding arc is loud and
Current setting may be too high.
Check setting and current output with ammeter.
spatters excessively.
Polarity may be wrong.
Check polarity against recommended polarity for electrode
being used.
Welder starts but fails
Wrong rotation.
Check rotation with the arrow on nameplate. If wrong
to generate current.
rotation, change the direction as follows:
a.
for three-phase---change any two leads.
b.
for two-phase, 3 wire---change two outside leads but be
sure neutral power line is connected to the motor neutral
(center terminal on the starter).
c.
for two-phase, 4 wire---change two leads in the same phase.
Generator brushes may be loose or missing.
Be sure that all brushes bear on the commutator and have
proper spring tension.
Series field and armature circuit may be open.
Check circuit with ringer or volunteer.
Poor welding lead connections.
Make sure all connections at work and machine are tight and
that there are no breaks in the welding leads.
Broken circuit in current control.
Replace current control.
Open rheostat.
To check for open rheostat, turn voltage to maximum. If
welder generates at maximum rheostat setting but not
below, replace rheostat.
Machine fails to hold heat
Rough or dirty commutator.
Commutator should be trued or cleaned.
constantly.
Brushes may be worn down to limit of
Replace or readjust brushes.
adjustments or life.
Brush springs may have lost adjustments
Replace springs.
or may be broken.
Field circuit may have variable resistance
Check field circuit with ammeter to discover varying
connection or intermittent open-circuit
current.
due to loose connection or broken wire.
Electrode lead or work lead connections
Tighten all connections.
may be poor.
Wrong grade of brushes may have been
DC-180-MK and 150J use Brush T-6968 (Lincoln part number)
installed on generator.
DC-250-MK and 200J use Brush T-7554.
Field rheostat may be making poor contact
Inspect rheostat and clean. If the rheostat finger is loose
and overheating.
replace rheostat.
Brush rocker may be loose or out of
Be sure the mark, half on
adjustment.
the rocker and half on the
bearing cage, is aligned.
-5-
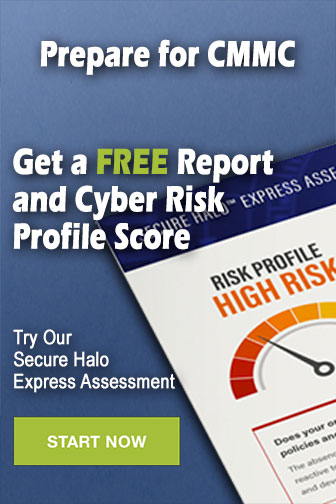