TM 55-1930-209-14&P-21
(8)
Inspect and open holes in spray nozzle. Blow dry compressed air through drilled oil passages in rod and
nozzle to make sure all passages are open.
(9)
Refer to Figure 6-28 for connecting rod magnetic particle inspection limits.
(10)
Refer to Table 1-1 and inspect connecting rod bushings for scoring, indications of overheating, or other
damage. Bushings that have overheated may become loose and creep together, thus blocking off lubricating oil to piston
pin bushing and spray nozzle.
(11)
Replace piston pin bushing and spray nozzle as follows:
(a) Remove piston pin bushing by driving bushing out with a suitably sized remover.
(b) Remove spray nozzle from connecting rod by placing nozzle remover tool inside connecting rod and
suspend both over a slotted support. Use a short hollow drift placed over nozzle and drive connecting rod down on tool.
Nozzle will be pushed out top of connecting rod.
NOTE
Orifice in lower end of drilled passage in connecting rod is not serviced separately, and it
is not necessary to remove it when replacing spray nozzle.
(c) Install new oil spray nozzle with holes positioned straight into counterbore in top of connecting rod.
Support connecting rod in an arbor press. Then, place a short 3/8 inch ID sleeve on top of spray nozzle and press spray
nozzle in connecting rod.
(d) Clamp upper end of connecting rod in holder so that bore of bushing is aligned with hole in base of
installation tool.
(e) Drive bushing into connecting rod bore with joint at top of rod.
(f) Turn connecting rod over in holder and install opposite bushing in same manner.
NOTE
Bushings must withstand an end load of 2000 pounds after being installed.
(12)
Refer to Table 1-1 for dimensions and ream piston pin bushing as follows:
(a) Clamp reaming fixture in a bench vise.
(b) Place crankshaft end of connecting rod on arbor of fixture. Tighten nuts on 3/8 inch-24 bolts to 40-
45 Ib-ft torque.
(c) Slide front guide bushing (pin end facing out) in fixture.
(d) Install a spacer in fixture.
6-62
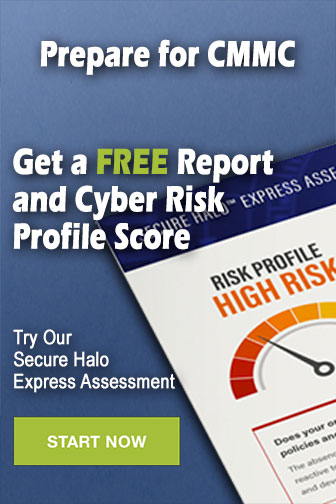