FORM 5S1408
AIR COMPRESSORS
2433
2570
5815
COMPRESSED AIR SYSTEM TERMINOLOGY
CFM - Cubic Ft. per Min. A measure of a compressors capa-
Constant Speed Control releases (unloads) excess pres-
city, and of the air flow requirement of air-driven devices. Com-
sure, while compressor operates continuously. Used in appli-
pressors have two ratings: Displacement CFM and Free Air
cations where air usage is continuous, or maximum air usage
CFM. Air-driven devices are rated in Free Air CFM.
exceeds 50 of the compressors capacity. See Unloaders.
Displacement CFM is calculated by multiplying the volume
Dual Control allows the selection of either constant speed
of the pump cylinders (low-pressure cylinders only on two-
or start-stop operation to fit varying air demands. Allows com-
stage pumps) by the pump speed in RPM. This rating does
pressors to be used efficiently in all applications.
not consider the efficiency of the air pump.
ently in all applications.
Free Air CFM is the actual air delivery of a pump to tank.
Check Valve. Allows air to flow one way only, from pump to
compressor, as measured when discharged to atmospheric
tank. When compressor stops, this valve closes, preventing
pressure.
loss of air from tank or damage to pump valves.
Pressure (PSI) - The force exerted by the compressed
Safety or Relief Valve vents the tank if excess pressure
air. Measured in lbs. per square inch (PSI).
builds up. For safety, a relief valve must be used on all
Air Pump (Compressor Head) - The part of the compressor
compressors. ASME stamped and sealed safety valve must
that compresses the air.
be used on all ASME tanks.
Single-Stage type, for applications requiring air at 100
Unloaders - There are two basic types:
PSI or less. Has one or more cylinders, all discharging
Head Unloaders open the air discharge line between
directly into the tank.
pump and tank, whenever the pump stops, relieving pressure,
Two-Stage type, for applications requiring air at 100-175
to make restarting easier. A check valve prevents loss of air
PSI. Has two or more cylinders in series. The first cylinder
from the tank. There are 3 types of head unloaders:
compresses air into the second cylinder, which compresses
Centrifugal: a speed-activated valve that closes as
it further, and then pumps it into the tank.
compressor comes up to speed and opens when compressor
Intercooler - A length of tubing, often with fins, connecting
stops.
the low and high pressure cylinders of a two-stage compressor
Pressure Switch Unloader works together with pressure
stage compressor pump. It is used to dissipate some of the
switch. Opens a valve to vent air whenever switch stops com-
heat generated in compressor, improving pump performance
pressor. Closes valve when switch restarts unit.
and life.
Combination Unloader and Check Valve (e.g., Load
Intake Filter - A foam pad or other filtering material mounted on
Genie, Nos. 4X996 to 4X999). As pump stops, valve senses
the pump air intake, to prevent airborne contaminants from
lack of air flow and relieves pressure in discharge line. As
entering the pump and reducing piston and cylinder life. Must
pump starts, vent closes and check valve reopens.
be serviced regularly for best pump efficiency.
Constant Speed Unloaders allow pump to operate unloaded
Air Tank (Receiver) - Stores air compressed by pump for peak
operate unloaded (running, but not compressing air) when tank
loads or intermittent use. Isolates pump pressure pulsation.
reaches pre-set level. Used on continuous run compressors.
3 types are available:
2 types:
ASME Standard (UM Type) Tanks. Made and tested in
Pilot Valve Unloader hold pump intake valve open when
accordance with American Society of Mechanical Engineers
pre-set pressure is reached.
standards. ASME certificate of compliance is furnished with
Load Genie Continuous Run Unloader (Nos. 5X709 to
each unit.
5X994) vents pump discharge line to the open air whenever
ASME National Board (U Type) Tanks. Made, tested,
tank pressure reaches pre-set level. Also acts as a check
inspected and registered to meet standards of ASME. A certi-
valve.
ficate is supplied with each tank to show compliance and
registry number. The ASME certificate is required by law in
AIR COMPRESSOR ACCESSORIES
many cities and states to pass safety codes. It assures that
(1) Code approved materials are used, (2) Steel plate is without
Magnetic Starter. An electrically operated switch used to
defects and is the specified thickness, (3) Proper welding
control the compressor motor and provide thermal protection.
techniques are employed by experienced operators, (4) Open-
Activated by the pressure switch.
ings and supports are the correct size, and (5) Tank has
Automatic Tank Drain Valve (No. 2Z166). Installed at
passed rigid tests. ASME tanks must be used where OSHA
bottom of tank; opens briefly during each pumping cycle to
and similar standards is not required.
release moisture condensed from the air.
Non-Code tanks do not meet ASME standards. They are
Belt Guard. Metal or plastic shield around pump flywheel,
widely used on small compressors in locations where compliance
belt and motor sheave to prevent hands or clothing from
with OSHA and similar standards is not required.
from getting caught in moving parts. Recommended for all
Tank Pressure Controls - three types used:
installations. Necessary to comply with OSHA requirements.
Pressure Switch Control starts and stops the compressor
Low Oil Level Shutdown Switch. Installed in compressor
as pressure falls and rises in the tank. Generally used on com-
crankcase and wired to magnetic motor starter.
pressors for intermittent duty and where maximum air usage
is less than 50. of the compressors capacity.
AIR SYSTEM COMPONENTS TERMINOLOGY
Filters. A device connected into the air line to trap solid or liquid
Aftercoolers remove water vapor from the compressed air by
particles that can damage tools, contaminate sprays.
lowering the temperature of the air and causing the water vapor to
Pressure Regulator. An adjustable valve used to reduce air
condense into droplets for easy removal. They can be piped
pressure from tank level to that required by air-using equipment,
between the pump and tank on the air compressor. There are two
and maintains it automatically. May be installed at the tank or at
types:
the connection for the air-operated equipment.
Watercooled uses water to cool the compressed air.
Lubricator . A device for constant feeding of oil mist into the air
Aircooled uses the ambient air to cool the compressed air.
powered equipment or tools. Not used for spraying applications.
Refrigerated Air Dryers reduces the compressed air tempera-
Air Cleaning Equipment. Air taken from the atmosphere by the
ture as low as 35oF to remove greater amounts of water than after-
compressor also contains many impurities including water vapor,
coolers. Inlet air temperature should not exceed 120oF. Piping
dust, oil and smoke. These contaminants can cause rapid water,
dryers closer to the work allows for cooling only that portion of air
clogging and malfunctioning of air tools, cylinders and valves. The
needed to do a specific function. Total system air need not be
following types of air cleaning equipment will help insure the efficient
cooled if dry air is not needed. Air or water cooled aftercoolers
performance of air-operated equipment.
may be used to precool compressed air before it enters the dryer.
GUIDE TO PLACEMENT OF AIR SYSTEM COMPONENTS
Proper equipment placement in a compressed air system assures
maximum efficiency and long life. For example, a compressed air
filter works best when located as near as possible to point at which
air is working. This minimizes the chances of air picking up addi-
tional contaminants, such as pipe scale.
Loop System (see diagram) allows best supply of air to work
stations as air can approach from two directions and not be drawn
off by prior work stations, as often happens on straight line systems
that dead-end.
Fig. 3
Log (see diagram) is the piping from main line to work station.
Take-off should be from top of pipe down to work station, which
should have a tee with drain valve or trap extending below tee to
take away contaminant.
PIPING REQUIREMENTS FOR AIR DISTRIBUTION SYSTEMS
Pipe size used should be large enough to keep the pressure drop
between the tank and the point of use to a minimum. All piping should
slope to an accessible moisture drain point.
The main air line should not be smaller than the compressor outlet
size. For long lines, sizes shown at right are recommended.
Outlets should be taken from the top of the main line (tees facing
up) to keep moisture out.
Check all piping and fittings regularly to avoid leaks in the system.
Filters, regulators and other accessories described above should also
be properly maintained.
VOLUME OF AIR FOR CYLINDERS
AIR FLOW (CFM)
THROUGH ORIFICE OR JET
In cubic feet for single acting. For double acting, multipy by 2.
Multiply by cycles/minute to get CFM.
Fig. 2
- 2 -
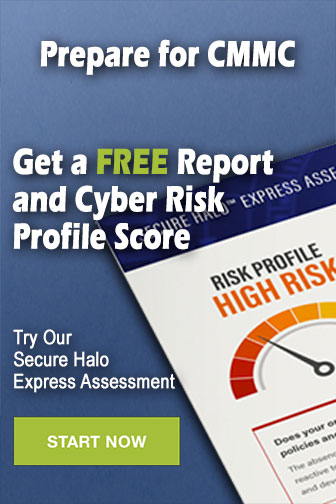